Can metal cutting fluid be used to process glass? Today, when optical glass and mobile phone glass are widely used, glass processing fluids have also become popular. Take the product of glass cutting fluid for example. There were many cutting fluid companies that used metalworking fluids before, but none of them specialized in glass processing fluids, so they would encounter various types of cutting fluids when using them. problem. Today I will discuss with you the difference between metal cutting fluid and glass cutting fluid.
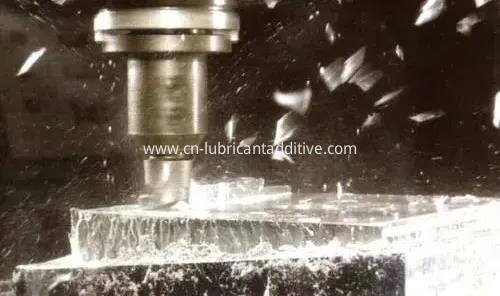
First, let`s take a look at the main ingredients and uses of the two cutting fluid products. The main components and functions of metal cutting fluid. 1. Metal cutting fluids are generally divided into A. Water-soluble cutting fluid B. Emulsion C. Cutting oil The formula of each cutting fluid product is extremely complex, and the composition of the product is also different for different metal materials. 2. The main components of metal cutting fluid A. Oily additives and extreme pressure additives; the role is to penetrate and lubricate in the processing of metals, reduce the tension of the interface between the metal and the cutting fluid, and prevent damage to the metal workpiece. B. Anti-rust additives, mainly to prevent machine tools, cutting tools, and metal workpieces from being corroded. It is a very polar compound. C. Anti-mold additives, prevent bacteria from multiplying, and play a sterilization effect. D. Anti-foam additives to prevent excessive foam in the processing of metal workpieces, which will affect the processing effect. E. Emulsifier, which allows the oily cutting fluid to be oriented and adsorbed on the oil-water interface, reducing the interfacial tension between oil and water 3. So what is the role of metal cutting fluid? A. Cooling effect; because when processing metal workpieces, the tool will generate strong friction with the metal workpiece, which will generate high heat, which will cause problems such as deformation and damage of the workpiece. B. Lubrication is always used; in the process of processing metal workpieces, strong friction will be generated on the surface of the tool and the workpiece, and the cutting fluid is the lubricant to reduce this friction. Thereby reducing the scrap of tools and metal workpieces. C. Cleaning function; cleaning produces iron powder, abrasive dust, oil stains and other dirt in the process of processing metal workpieces. These dirts are easily adsorbed on the surface of metal workpieces, tools, and grinding wheels, and affect the cutting effect. D. Anti-rust effect; prevent the cutting fluid from corroding metal workpieces and machine tools during the processing process. If there is no anti-rust function, it will cause corrosion of the workpiece and affect the effect. At present, most metal cutting fluids will add rust inhibitors. The main components and functions of glass cutting fluid. 1. Glass cutting fluid is mainly divided into two categories A. Optical glass cutting fluid This type of cutting fluid is mainly used for the processing of precision glass components such as optical glass, camera lenses, LCD glass panels, and optical instruments. B. Mobile phone glass cutting fluid Due to the rise of mobile devices, glass cutting fluids have also been subdivided. Such cutting fluids are mainly used for mobile devices such as mobile phone glass cover, tablet computer glass, and smart watch glass panel. 2. The main components of glass cutting fluid It is compounded with various additives such as borate, polyol, anionic surfactant, lubricant, rust inhibitor, etc. Its characteristics are that it does not contain mineral oil and animal oil, the product will not decay, it is easy to store, and has a long service life. . Most of the water-based glass cutting fluids and oily glass cutting fluids are not easy to clean, and few people can use them. 3. The role of glass cutting fluid It is mainly used for cutting glass and edging the glass.
First of all, it plays a role of lubrication. Glass is a very fragile product. If the lubricity is not good, it will cause problems such as chipping and cracking.
The second is to play the role of cleaning. In the process of processing glass workpieces, dirt such as glass powder and grinding powder will be generated, which must be cleaned in time to prevent adhesion to the glass surface and affect the processing effect.
The third is to play the role of sedimentation. During the process of processing glass workpieces, the grinding powder generated should settle to the bottom of the machine in time to prevent the glass workpieces from being worn during the use of cutting fluid, resulting in scratches and breakages of the glass workpieces, etc. problem.
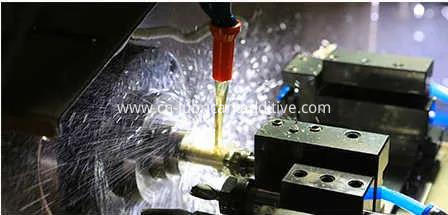
The specific difference between metal cutting fluid and glass cutting fluid After the above analysis, everyone should have a certain understanding of the two cutting fluids, both in terms of formula and function. Therefore, choosing the right cutting fluid product is very important for companies that produce glass cover plates. Therefore, metal cutting fluid cannot be used to process glass, but now many unscrupulous companies use metal cutting fluid to make a little improvement and start to market, causing many companies to have various problems.