In the process of lathe processing, the filtration of cutting oil has always been a more difficult problem. Many incorrect oil filtration methods will cause the waste of cutting oil, or the incomplete filtration will affect the processing efficiency, or even damage the tool, etc. A brief description of how to filter the cutting oil during machining. The filtration treatment of machine tool cutting oil includes three aspects: ①Remove the chips from the processing area; ② Transport the chips outside the system; ③ Separate the chips from the cutting oil.
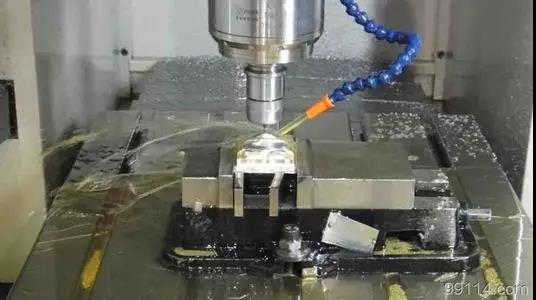
1. Chip removal There are several ways to remove chips from the machining area: (1) The chips are thrown out by gravity or the centrifugal force of the tool rotation, and fall on the chip conveyor belt under the machine tool by the weight of the chips. The bed structure should be easy to remove chips, such as tilting the bed or placing the machine tool on an inclined base, and using a chip baffle or a protective plate to completely seal the processing space to prevent the chips from flying, making it easy to gather and easy to remove, and at the same time It also makes the environment safe and tidy. (2) Rinse the processed parts with a large flow of cutting oil to wash away the chips, and then use a filter to separate the chips from the cutting oil. (3) Use compressed air to blow chips. (4) Vacuum chip suction is used. This method is most suitable for dry grinding process and powdery chips formed during processing of brittle materials such as cast iron. A vacuum suction pipe connected to the main suction pipe is installed near each processing station. 2. Chip transportation The chip conveyor is generally set in the trench under the machine bed, and the chips and cutting oil discharged from the processing area directly fall into the trench and are transported out of the system by the chip conveyor. Chip conveyors have mechanical, fluid and air pressure types. The mechanical type has a wide range of applications and is suitable for various types of chips. There are many types of mechanical chip conveyors, among which flat chain, scraper and spiral chip conveyors are more common. (1) Flat chain chip conveyor; the steel flat chain belt hauled by the roller sprocket runs in a sealed box, the chips in the process fall on the chain belt and are taken out of the machine tool, and the chip hopper is transported by the AGV In the chip collection area, the chips are pressed into blocks for transportation. This kind of chip conveyor is generally equipped with one for each machine tool. When used on a turning type machine tool, it is often integrated with the machine tool cutting oil tank to simplify the machine tool structure.
(2) Scraper-type chip conveyor The enclosed chain is mounted on two sprockets. The scrapers welded on both sides of the chain scrape the cutting chips and cutting oil in the trench to the underground oil storage tank, and the hoist lifts the chips into the transport vehicle and transports them away. The lower chain is supported by the supports that run through the entire line, so that the scraper does not contact the bottom of the groove. In order to prevent the upper chain from sagging, use the upper support to support it. The driving wheel should be determined according to the direction of scraping to ensure that the lower edge of the chain is tight. The double conveying groove is used for the sorting and conveying of black and colored chips. The chip shunt baffle in the groove controls the black or colored chips to enter its collection hopper separately to avoid mixing of different chips, thereby increasing the value of waste.
(3) Spiral chip conveyor; The motor drives the screw rod installed in the chip flute through the deceleration device. When the screw rotates, the chips in the groove are pushed by the screw rod to move forward continuously, and finally discharged into the chip collection box. There are two types of spiral rods, one is rolled into a spiral spring with a flat steel strip; the other is a spiral piece welded tightly on the shaft. The screw-type chip conveying length can be adjusted, and the screw can be connected section by section. It is often set on one machine tool, or set on several machine tools, and it can also run through the entire line. Spiral chip conveyor has simple structure, small space occupation and good chip removal performance, but it is only suitable for horizontal or small-angle inclined linear chip removal, and cannot be inclined, lifted or turned to remove chips at a large angle. 3. Chip separation (1) Discharge the chips and cutting oil to the cooling station. When it passes through the orifice plate or the screen, the cutting oil leaks into the sedimentation tank, passes through the labyrinth partition and filter to further remove the suspended debris, and then is pumped back into the pressure main line. The chips left on the orifice plate can be discharged and concentrated by scraper type chip removal and chip conveying devices.
(2) Chips and cutting oil are directly sent into the sedimentation tank together, and then the chips are transported out of the tank with a chip conveying device. This method is suitable for automatic chip removal situations where the cutting oil is flushed with the chips. For the treatment of extremely fine chips or abrasive chips, electromagnetic belt-type chip conveyors are generally used in the cooling station to suck the chips or dust on the belt and send them out of the pool. It is very difficult to separate fine aluminum scraps from the floatation tank because they are not easy to settle. Special paper or cloth filters, paper or cloth tapes can be used to continuously wrap from one roller to another. On the surface of the belt, so as to continuously remove the debris deposited on the surface of the belt. The correct way of lubricating oil filtration or effective protection of the cutting tool can make the lathe work stably and improve the quality of the workpiece. Please be sure to perform the filtering operation in accordance with the instructions of the lathe.