Maintenance and maintenance methods of spindle bearings
July 11, 2022
DZ series spindle bearings are mainly used for textile machinery spindles for cotton, wool, linen, silk, chemical fiber, pure spinning and blended spinning machines and twisting machines. For cotton spinning enterprises, how to better use, maintain and maintain these special parts is very important.
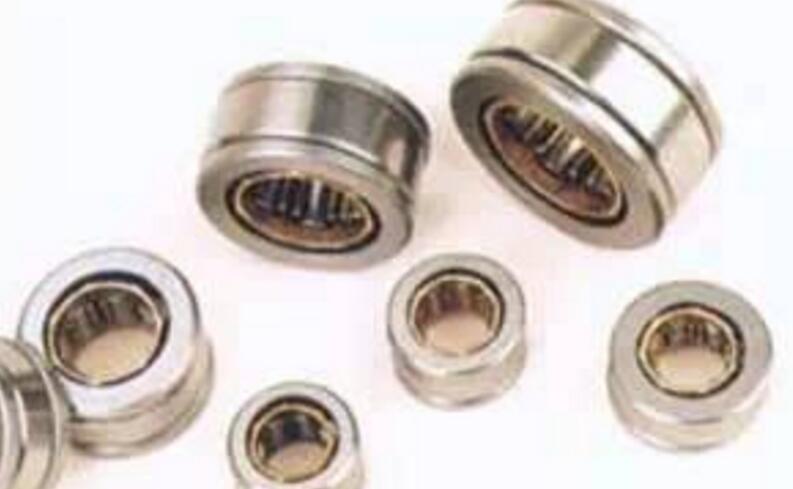
Here, we mainly talk about some methods and suggestions on the use, maintenance and maintenance of spindle bearing series products from the perspective of product manufacturers and combined with the use of users. 1. Performance and characteristics of spindle bearings Spindle bearing, as a special bearing for textile, has a special structure. It adopts a single-row radial short cylindrical roller structure without inner ring, and is a high-speed precision bearing that can bear pure radial load. The assembled integral bearing is still in an open state. Considering the needs of assembly, packaging, transportation and reassembly by the user, a special anti-rust oil is mainly used for the spindle bearing at present. It not only has good anti-rust performance, but also can ensure that the bearing is not easy to scatter when entering the final user assembly link. Due to the single row of short radial rollers, this series of bearings has strong rigidity and can withstand large radial loads; high manufacturing precision, flexible and stable rotation, low noise, suitable for high-speed operation; simple structure, low power consumption; maintenance is more convenient . At present, the implementation standard of spindle bearing series products is still: FZ/T92025-1994 "DZ series spindle bearing" textile industry standard. The cage using the new reinforced nylon material has the following performance characteristics: 1. The new cage adopts engineering plastic - PA66 glass fiber reinforced nylon material; 2. Using the injection molding processing method, the cage has better manufacturability, and the stability of size and shape is also good; 3. The cage made of nylon material has a certain self-lubricating effect; 4. By optimizing the design of the pocket structure, the swing amplitude of the rollers during high-speed operation can be reduced, thereby reducing noise to a certain extent. Second, the correct use of spindle bearings First of all, if the size, shape and accuracy of the assembly hole of the bearing housing are not good, the bearing will be affected by it and cannot exert the best performance. For example, if the dimensional accuracy and shape accuracy of the inner hole of the bearing seat of the matching parts are not good, the outer ring of the bearing will be deformed, which will lead to the deterioration of the roundness of the inner hole of the bearing; The load will reduce the fatigue life of the bearing, and will cause the cage to be damaged and sintered more seriously; if the accuracy of the spindle bearing gear of the inner ring of the bearing is not good, such as size, roundness, cylindricity, waviness, roughness, and position. Accuracy in other aspects will also obviously lead to an increase in the vibration value of the entire set of spindles. Secondly, the complete set of bearings undergoes strict and precise matching before assembly, so the scattered bearing parts cannot be used interchangeably without re-measurement and matching before use. Third, on the cleaning of spindle bearings and spindle feet. Due to the compact structure of the spindle foot, there are many other parts in the spindle foot cavity, and their cleanliness will also affect the cleanliness of the bearing working cavity. Therefore, it is a more reasonable process to use the pre-cleaning of the spindle foot parts before the assembly, and then fine-clean the spindle foot of the assembly including the bearing after the assembly is assembled. Fourth, the bearing should not be bumped and impacted during assembly, which can easily cause collision between bearing parts and cause the bearing to fail. Fifth, when the bearing seat is crimped, attention should be paid to controlling the angle, strength and other factors of the crimping, so as to avoid the deformation and failure of the bearing parts caused by the unreasonable crimping. Sixth, for bearings that have exceeded the rust-proof period or have been stored for a long time, rust may occur or the rollers may stick to death due to drying of the rust-proof oil. 3. Correct maintenance and maintenance methods of bearings First of all, when the spindle bearing in the spindle is running, it must be fully lubricated, and lubricating oil should be added regularly according to the actual use conditions, and the oil should not be cut off for a long time. Therefore, for user enterprises, better and more suitable spindle lubricating oil should be selected. The new special spindle oil can significantly improve the lubricating performance, prolong the oil change interval, prolong the service life of the spindle and the bearing, and also have better anti-rust and anti-corrosion properties. Secondly, the bearing with reinforced nylon cage should be used at a temperature lower than 120 ℃, and it is strictly forbidden to cook and clean it. In addition, attention should be paid to the method when the spindle is maintained and cleaned to prevent damage and scratches on the surface of the rollers. To remove the residue on the bearing part as much as possible, it is better to use the method of washing and suctioning the residual oil inside the spindle foot. Pay attention to avoid the use of dumping type, so that cleaning waste accumulates and remains in the bearing part, resulting in problems such as noise, wear and failure of the bearing.