As an indispensable basic component in industrial power transmission, gearbox is widely used in various mechanical transmission fields. In recent years, the application scenarios of gear boxes in downstream industries such as wind power and metallurgy have become increasingly rich and diversified. Customers have increasingly high requirements for the accuracy, variety and quality stability of gear box products. The importance of product quality and technical level of gear boxes has become increasingly prominent.
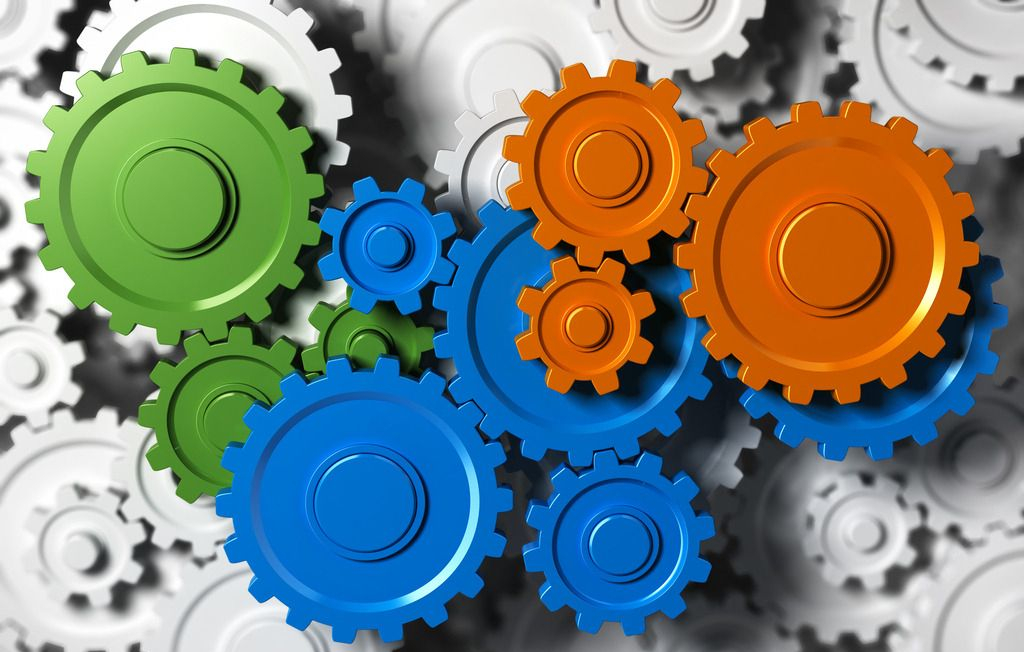
In this context, the manufacturing enterprises of gear boxes continue to increase investment in research and development and independent innovation, strengthen quality control, and promote new product development and upgrading. Among them, the focus is on the research of basic technologies such as gear tooth profile and gear bearing capacity, so as to make the gearbox develop towards higher load, greater power and smaller volume to adapt to the changing market demand. It is typical that the torque density (rated torque of motor shaft output per unit volume) of the gearbox is increasing, as shown as below.
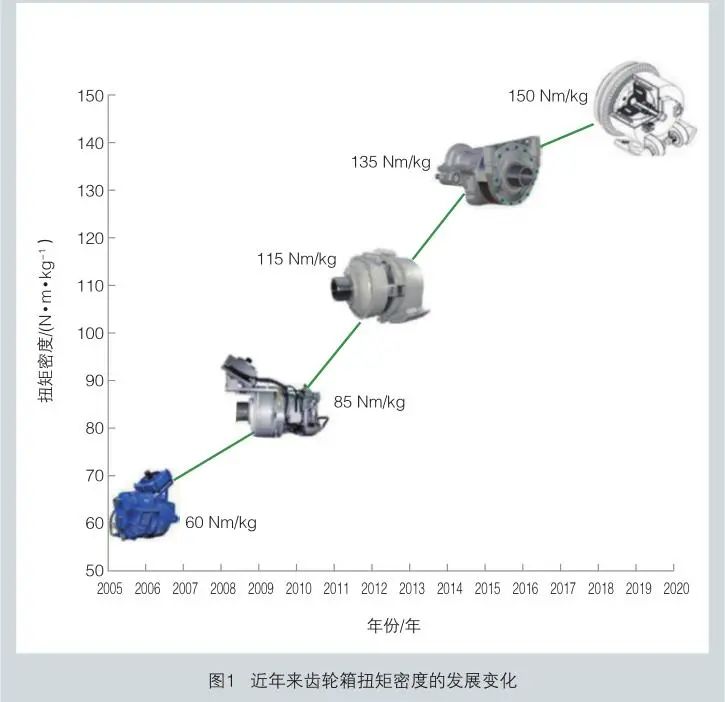
With the continuous development of the gear box industry, the working conditions of the equipment are more stringent, and the performance requirements of industrial Gear Oil are also increasingly stringent: the increase of load increases the contact pressure of the tooth surface and the wear and pitting between metals; Moist working conditions will lead to increased bearing corrosion; The smaller size of the gearbox means that there is less oil for lubricating gears and bearings, which will lead to the increase of oil temperature and accelerate the oxidation of oil. The result of oil oxidation is that the oil color becomes darker, viscosity increases, acidic substances increase, and precipitation occurs. These acidified fission compounds will bring a series of adverse effects on the use of oil products, such as corrosion of metals and blockage of oil lines, which will greatly shorten the service life of oil products and gearbox components and increase the cost of equipment maintenance and replacement. Therefore, it is an inevitable trend to further improve the anti-oxidation performance of oil products. At present, the industrial gear oil mainly adopts the long-term oxidation resistance test method, which takes a long time, causing the inconvenience of gear oil research and development and actual production. This paper attempts to explore a rapid test method for the oxidation resistance of industrial gear oil, in order to facilitate oil development and factory production. Oxidation mechanism of industrial gear oil and test method for oxidation resistance Oxidation mechanism of oil products After nearly 50 years of research, the oxidation of organic materials, including polymers, is generally considered to be the self oxidation reaction process of branched chains of free radicals (Fig. 2). The increase of atmospheric oxygen, ambient temperature and some metal ion impurities will accelerate this oxidation reaction: Chain initiated reaction: R-H——R•+•H R-R——R•+R• ROOH——RO•+•OH Chain growth reaction: R•+O2 ——R-O-O• R-O-O•+R-H——ROOH+R• R-H+RO•——R•+ROH R-H+•OH——R•+H2O Chain termination reaction: ROO •+R • - non radical product ROO•+ROO• R•+R•
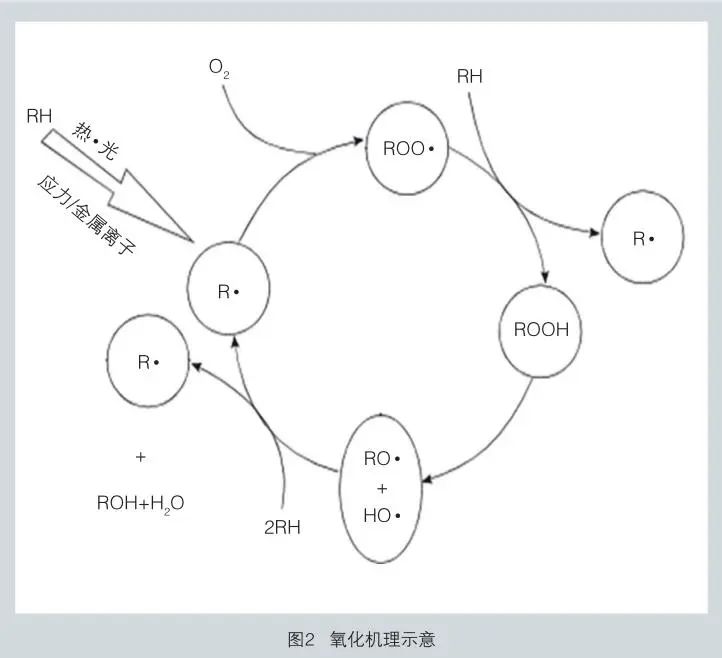
Specifically, under the action of light, heat and transition metals, lubricating oils (including industrial lubricating oils) produce free radicals, which react with oxygen to produce peroxy [ROO •], and peroxy reacts with other molecules to produce hydrogen peroxide [ROOH] and free radicals [R •]. Hydrogen peroxide is further decomposed to produce oxidized free radicals [R •] and peroxy radicals [ROO •]. As a result of chain reaction, ketones, aldehydes and organic acids are finally generated. Finally, condensation reaction is carried out to generate sludge and paint film, and at the same time, the viscosity of lubricating oil is increased. In order to inhibit the oxidation of oil products, you can choose to capture free radicals or decompose peroxides to obtain stable compounds. Among the commonly used antioxidants, phenolic and amine antioxidants are effective in capturing free radicals and are free radical terminators; ZDDP (zinc dialkyl dithiophosphate) and thioene are mainly used to decompose peroxides, which are typical peroxides decomposing agents.
Used for industrial gear oil test method and comparison of oxidation resistance For the specific working conditions of industrial gear boxes, SH/T 0123 is usually used in the industry to determine the oxidation performance of industrial gear oil. The specific method is: at 121 ℃, continuously inject constant pressure dry air (167 mL/min ± 8.3 mL/min) into the oil. After 312 h of the test, test the 100 ℃ viscosity growth and sedimentation value change of the oil. At the same time, the testing methods for the oxidation performance of lubricating oil mainly include rotating oxygen bomb test (ASTM D2272), inhibiting mineral oil oxidation test method (ASTM D943) and extreme pressure lubricating oil oxidation performance test method (SH/T0123). The differences of these methods mainly depend on the working conditions of mechanical equipment. The corresponding oxidation methods of different equipment are different. The specific differences include temperature, whether air is connected, whether metal catalyst is added, etc. Different researchers tried to use different oxidation performance testing methods to test the oxidation resistance of industrial gear oil (or other oils). Wen Yanlong used DKA oxidation stability test (CEC L-48) to investigate the effect of dispersant on the oxidation performance of heavy load vehicle gear oil; Zhou Kang compared the test results of DKA oxidation test (CEC-L-48-A-00), oven oxidation test (self built) and SH/T 0123 method, which took a relatively short time. He found that the results of DKA oxidation test and self built oven oxidation test were consistent and differentiated, and had a strong correspondence with the test results of SH/T 0123; Li Jiusheng used high pressure differential scanning calorimetry to evaluate the effect of antioxidants on the oxidation stability of lube Base Oil. In the latest GB 5903-2011 Industrial Closed Gear Oil, L-CKC and L-CKD industrial gear oils are required to use SH/T 0123 to determine the oxidation performance of oil products, mainly because the test method of SH/T 0123 is closest to the working conditions of industrial gear oils. However, the DKA oxidation test, self built oven oxidation test and high pressure differential scanning calorimetry used in the literature are obviously different from SH/T 0123: the air inflow of DKA oxidation test is 83 mL/min, and there are metal catalysts in some tests; The self built oven oxidation test is a confined space, and there is no stable air flowing into the oil; High pressure differential scanning calorimetry heats the thin oil film in the metal sample pool (mostly aluminum material) under oxygen atmosphere, and detects the heat released by the oil due to oxidation to judge the anti-oxidation performance of the oil. However, this method uses high pressure and high oxygen content conditions, which is quite different from the actual working conditions of industrial gear boxes. Therefore, at present, when testing the oxidation resistance of industrial gear oil, there is a lack of an inspection method that takes a short time and is similar to the operating conditions of industrial gear oil. Based on this, this paper attempts to study the rapid test of the oxidation stability of industrial gear oil using enhanced oxidation test. Acceleration principle of oxidation reaction and enhanced oxidation test plan In the research field of physicochemical reaction efficiency, the chemical reaction rate generally follows the Arrhenius formula:

In formula (1), k1 and k2 are rate constants, R is molar gas constant, T1 and T2 are corresponding thermodynamic temperatures, and Ea is apparent activation energy. In 1889, on the basis of summarizing a large number of test results, Arrhenius proposed an empirical formula for the relationship between chemical reaction rate constant and temperature. According to this formula, assuming that the activation energy Ea is a constant independent of temperature, then within a certain temperature range, the reaction rate will be doubled for every 10 ℃ increase in temperature. Long term practice has proved that the formula has a wide range of applications, and is applicable to gas phase reaction, liquid phase reaction and most complex catalytic reactions. It is not only a basic reaction, but also a part of complex chemical reactions. According to a large number of literature studies, the oxidation reaction of industrial gear oil is a free radical chain reaction, so the oxidation reaction of industrial gear oil can also refer to the Arrhenius formula, that is, the reaction rate will be doubled when the temperature rises by 10 ℃. Considering that some antioxidants will promote the oxidation reaction when the temperature is too high, SH/T 0123 is a method that has experienced a long time and a lot of practical experience; Therefore, considering the balance between test time and antioxidant performance, it is proposed to establish an enhanced oxidation test scheme based on SH/T 0123, in which the test temperature is 151 ℃ (121 ℃ is increased by 30 ℃, and the oxidation reaction rate is accelerated by 8 times), and the reaction time is one eighth of the original time (312 h), that is, 151 ℃, 39 h, to preliminarily judge the anti-oxidation performance of gear oil in a short time. Oxidation resistance of industrial gear oil research on fast test method Test oil and physical and chemical properties The test oil is L-CKD industrial gear oil with certain gradient oxidation resistance selected on the same base oil system; In order to increase the reliability of the data, the lowest and highest viscosity grades among the commonly used viscosity grades of industrial gear oil are specially selected, namely three L-CKD 150 and three L-CKD 680 oils. See Tables for oil formula and for physical and chemical analysis as below.
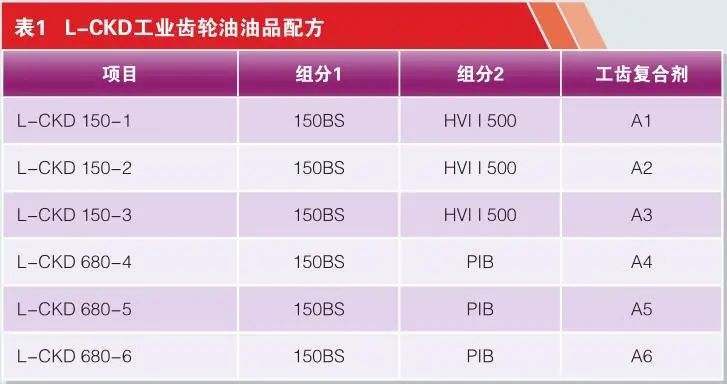
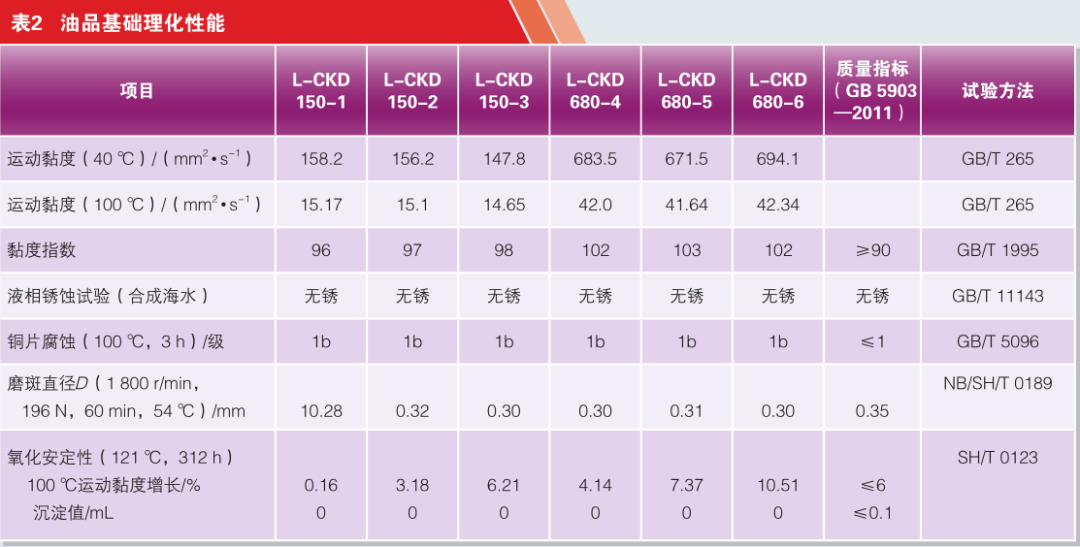
It can be seen from Table that with basically the same formula of base oil system, the conventional physical and chemical properties of the investigated samples are roughly the same, which is conducive to minimizing the impact of other variables, so as to maximize the accuracy of test results. In addition, although the oxidation stability indexes of sample 5 and sample 6 have exceeded the requirements of GB 5903-2011 (no more than 6%), they are also subject to intensive oxidation tests. This is mainly to expand the investigation scope of oil oxidation performance and make the data chain more complete. Oxidation stability test, enhanced oxidation comparative analysis of test results The results of oxidation stability test and enhanced oxidation test of the above six L-CKD industrial gear oils are shown in Table 3100 ℃ kinematic viscosity growth comparison as shown in Figure as below.
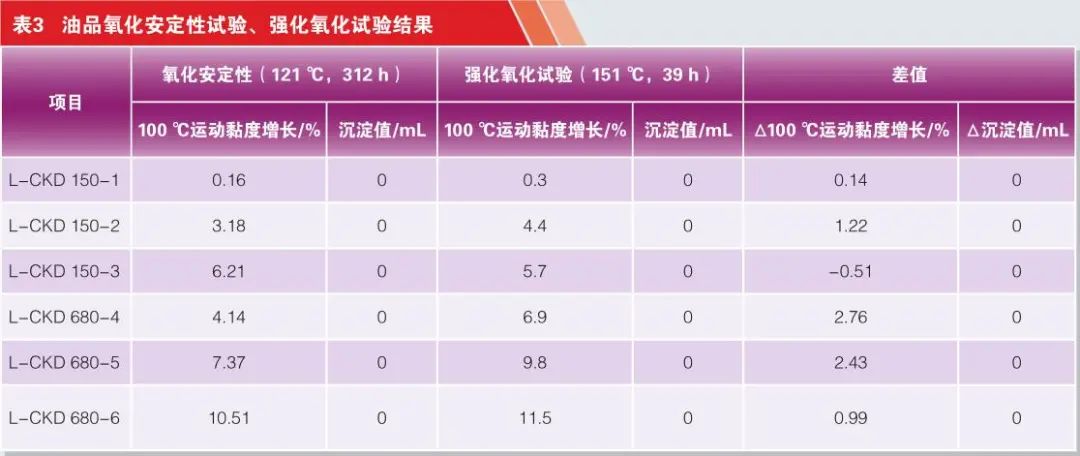
It can be seen that: In the viscosity grade of L-CKD150, the difference of oxidation data of L-CKD150-1, L-CKD 150-2, and L-CKD150-3 gear oils at 151 ℃ and 121 ℃ is small, only -0.51%~1.22%, which indicates that the oxidation reaction process at 151 ℃ and 121 ℃ is roughly the same, and the trend and specific values show good consistency. In the L-CKD680 viscosity grade, the overall increase rate of oil kinematic viscosity after the enhanced oxidation test is relatively large, which may be due to the higher viscosity grade of the oil in the similar industrial gear oil formulation system, the more BS bright oil and viscosity index are used, the more polymer chains, resins and asphaltenes in the oil, and the easier it is to be cross-linked under high temperatures, leading to the further increase of oil viscosity and the poorer oxidation stability of the oil. Although the growth rate of the kinematic viscosity of the three oils L-CKD 680-4, 5 and 6 is on the high side as a whole, the trend of their kinematic viscosity growth rate is basically consistent under 121 ℃ and 151 ℃ oxidation. Therefore, the 151 ℃ enhanced oxidation test is still of certain reference value for rapid judgment of the oxidation performance of gear oil of this viscosity level. In actual operation, a known L-CKD680 gear oil with 121 ℃ oxidation stability and qualification can be selected as the standard sample, The general oxidation resistance of L-CKD680 gear oil to be tested was determined by fast oxidation test at 151 ℃. Conclusion: In this paper, an enhanced oxidation test based on SH/T 0123 was designed, and the rapid determination of the oxidation performance of industrial gear oil was preliminarily explored. It is found that the rapid test method has good consistency in low viscosity L-CKD150 industrial gear oil; In the high viscosity L-CKD680 industrial gear oil, the enhanced oxidation test result is larger than the oxidation stability test result, but the change trend is consistent, which can be used to preliminarily judge the range of oil oxidation performance indicators. In actual operation, it is recommended to add standard oil with known oxidation performance for comparison and judgment. This method can be used to preliminarily judge the general range of oil oxidation performance, greatly reducing the time cost in the oil inspection process, and has an important reference role for the preliminary inspection of gear oil additives and finished products.