Cutting fluid cooling you do not know the three methods!
March 19, 2023
When lubricating cutting fluid (such as cutting oil) is used, it should be transported to the place where oil film can be formed on the friction surface. On the contrary, if the selected cutting fluid is mainly cooling (such as water-based cutting fluid), the cutting fluid should be close to the edge of the tool. Under this condition, the cutting fluid is usually forced to enter the cutting area by pressure method, so as to take away the heat generated by friction and deformation of the tool, workpiece and chip. Continuous application of cutting fluid is better than intermittent application of cutting fluid. Intermittent application of cutting fluid will produce thermal cycle, which will lead to crack and edge collapse of hard and brittle tool materials (such as cemented carbide tools). Intermittent use of cutting fluid will not only shorten the tool life, but also make the working surface rough and uneven. Another advantage of using cutting fluid correctly is to effectively remove chips, which also helps to prolong tool life. If the nozzle of cutting fluid is properly placed, the chip removal groove of milling cutter and drill bit can be prevented from being blocked or blocked by chips. For the processing of some large workpieces, or the powerful cutting and grinding with large feed, two or more rows of coolant nozzles are used to make them fully cooled, which is conducive to improving the processing efficiency and ensuring the processing quality.
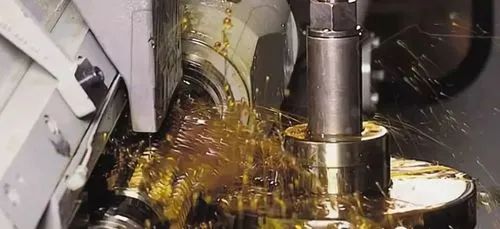
1. Manual fueling method for cutting fluid cooling Solid or paste lubricant can be coated or dripped onto the tool or workpiece with a brush or brush (mainly for tapping thread and die sleeve thread). Recently, a hand-held liquid feeder has been developed to atomize the lubricant through pressure and spray it onto the tool and workpiece. On machine tools without dosing cooling system, if the number of drilling or tapping is not large, manual oiling is an effective method. When two different processes are to be completed on the same machine tool, the manual oil can be used together with the overflow cooling system on the machine tool. 2. Cutting fluid cooling overflow method The most common method of using cutting fluid is overflow method. The cutting fluid is pumped into the pipe with a low pressure pump and flows out from the nozzle through the valve. The nozzle is installed near the cutting area. The cutting fluid flows through the cutting area and then flows to different parts of the machine tool, and then collects in the oil collecting pan, and then flows back to the cutting fluid tank from the oil collecting pan for recycling. Therefore, the cutting fluid tank should have sufficient volume to allow the cutting fluid to cool down and allow fine chips and abrasive particles to settle. Depending on the type of processing, the volume of the cutting fluid tank is about 20-200L, and the volume of the cutting fluid tank is larger for individual processing, such as drilling deep holes and strong grinding, etc. The cutting fluid tank can reach 500-1000L or more. A coarse filter shall be installed in the oil collecting pan to prevent large cutting from entering the cutting fluid tank, and a fine filter shall be installed at the oil suction port of the pump. For grinding, diffraction, deep-hole drilling, deep-hole boring and other machine tools, due to the high requirements for the surface quality of the processed workpiece, finer grinding debris, grinding wheel particles and cutting particles must be removed. For example, for gun drilling deep-hole processing, 10um filter paper should be used for filtering. The use of filtering equipment can avoid excessive pollutants or metal particles in the cutting fluid, which helps to keep the cutting fluid clean and prolong the service life of the cutting fluid. Modern automatic machine tools are generally equipped with cutting fluid filtration, separation and purification devices. The overflow method can make the cutting fluid continuously flow to the cutting area and wash away the chips. The flow of cutting fluid should be larger, so that the tool and workpiece can be submerged by the cutting fluid. In addition to providing proper cutting fluid to the cutting area, there should be enough cutting fluid to prevent abnormal temperature rise. In the process of deep-hole drilling, if the cutting fluid tank is too small, the temperature of the cutting fluid will rise rapidly. When the oil temperature exceeds 60 ℃, the cutting cannot continue. Therefore, deep-hole drilling machines are generally equipped with large cooling oil tanks. The distribution of cutting fluid flow directly affects the efficiency of cutting fluid. The nozzle should be positioned so that the cutting fluid will not be thrown away from the tool or workpiece due to centrifugal force. It is better to use two or more nozzles, one to send the cutting fluid to the cutting area, while the other is used to assist in cooling and washing away the chips. When turning and boring, it is required to send the cutting fluid directly to the cutting area, so that the cutting fluid can cover the cutting edge and workpiece and play a good cooling role. Practical experience has proved that the inner diameter of the cutting fluid nozzle is at least three quarters of the width of the turning tool. For heavy turning and boring, a second nozzle is required to supply cutting fluid along the lower side of the tool. The cutting fluid supplied by the lower nozzle can be smoothly delivered between the tool and the workpiece without being blocked by cutting, which is helpful for lubrication at low speed. When horizontal drilling and reaming, it is best to send the cutting fluid to the cutting area through the inner hole of the hollow tool, so as to ensure that there is enough cutting fluid at the edge and flush the chips out of the hole. Because the spiral groove of the drill bit (to discharge the chips) plays the role of discharging the cutting fluid from the cutting area to the outside, even for the vertical drill, there is very little cutting fluid entering the cutting area. Only the hollow drill bit can solve this problem.
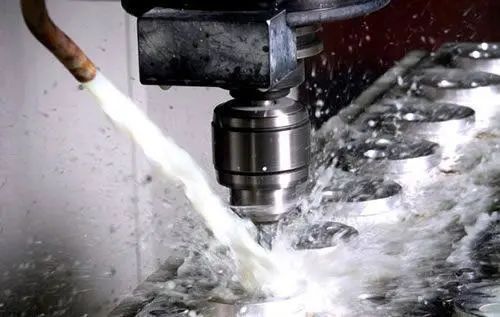
3. Cutting fluid cooling and high pressure method For some machining, such as deep hole drilling and sleeve drilling, high pressure (pressure is 0.69-13.79MPa) cutting fluid system is often used to supply oil. The deep-hole drill uses a single-edge drill bit, which is similar to boring, except that there is a path for cutting fluid inside the drill bit. Casing drilling is a method of drilling a cylindrical hole on the workpiece but leaving a solid cylinder. When the tool enters the workpiece, the drilled solid cylinder will pass through the hollow cylindrical cutter head and use the pressure pump to send the cutting fluid around the tool, forcing the chip to flow out from the tool center. The cutting fluid used for hole drilling must have good extreme pressure and anti-sintering properties, low viscosity to flow freely around the tool, and good oiliness to reduce the friction coefficient between the tool and the workpiece, and between the tool and the chip. The main problem of deep hole drilling is how to maintain sufficient cutting fluid flow in the cutting area. One way is to use the cutting groove as the cutting fluid channel. The cutting fluid pressure is 0.35-0.69MPa. The rotating sealing sleeve flows into the drill bit, and then directly into the cutting area. The cutting fluid flowing out of the hole helps to remove the chips. In deep hole drilling, using oil hole drilling is a great progress compared with overflow method, and the life and productivity of the bit have been greatly improved. High-pressure method is beneficial for the cutting fluid to reach the cutting area, and sometimes it is also used on other machine tools. Grinding makes the high-pressure nozzle beneficial to the cleaning of the grinding wheel.