Cutting fluid selection is right, accuracy and tool life "double"
February 05, 2023
In order to adapt to different processing requirements, there are many kinds of cutting fluids, which can be divided into water-based cutting fluids and oil-based cutting fluids according to chemical composition and state.
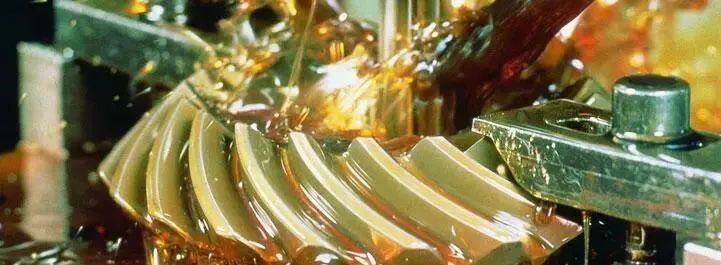
Generally, the cutting fluid diluted with water is called water-based cutting fluid, and the cutting fluid used without water dilution is called oil-based cutting fluid. Water-based cutting fluid Antirust emulsion Compared with oil-based cutting fluid, emulsion has the advantage of good cooling effect. Generally, the water solution diluted at 5%~10% has low cost and is safe to use. The biggest disadvantage of emulsion is its poor stability, easy to be eroded by bacteria and mold, and short service life Antirust lubricant and emulsion It has good lubricity. The disadvantage is that these animal and vegetable fats or long-chain unsaturated fatty acids are easy to be decomposed by microorganisms and molds, and the service life is very short. Extreme pressure emulsion With strong extreme pressure and smoothness, it can be used for heavy cutting, such as tapping, broaching and strip cutting, and also for the processing of difficult-to-cut materials such as stainless steel and heat-resistant alloy steel. Oil-based cutting fluid Grease oil proof (or oily additive)+mineral oil Grease anti-oil has strong adsorption on metal surface and good lubrication performance. Its disadvantage is that it is easy to oxidize and deteriorate, and forms a mucous membrane on the surface of the machine tool that is difficult to clean (i.e. "yellow gun"), which is generally used for precision machining of soft rod, gear hobbing, gear making, etc. Active EP cutting oil It has good anti-sintering performance and extremely long lubricity, can improve the service life of the tool under high temperature and high bed conditions, and has strong control ability to the chip accumulation of the tool. It is mainly used for cutting materials that are easy to gnaw and difficult to machine. Inactive extreme pressure cutting oil Good EP lubricity and non-corrosive to non-ferrous metals. It is easy to use and widely used in various cutting processes. Compound cutting oil The use of oily additives, such as advanced fatty acids and fatty oils, can produce physical and chemical adsorption on the metal surface, form a molecular film adsorption layer, which can reduce the friction resistance during cutting, maintain a good lubrication state in a wide range of temperatures, and is suitable for multi-station cutting and cutting of various materials. Select cutting fluid according to the tool Knowing the types and characteristics of cutting fluid, how can we match it with the tools we use everyday? High speed steel tool This material is a high-grade alloy steel based on chromium, nickel, tungsten, molybdenum, vanadium (some also contain aluminum). Their heat resistance is significantly higher than that of tool steel, and the maximum allowable temperature can reach 600 ℃. It has high toughness and is suitable for workpieces with complex geometric shapes and continuous machining. Besides, high-speed steel has good machinability and is easy to be accepted in price. Due to poor red hardness of high-speed steel tools, cutting fluid required 1. Oil-based cutting fluid or emulsion is recommended for low and medium speed cutting. 2. In high-speed cutting, water-based cutting fluid is preferred due to its large heat output. 3. Extreme pressure emulsion or extreme pressure cutting oil shall be used during finishing to reduce friction, improve surface quality and precision, and prolong tool life. If oil-based cutting fluid is used, more oil mist will be produced, which is easy to cause workpiece burn, machining quality decline and tool wear increase. In addition, extreme pressure water solution or extreme pressure emulsion is recommended for rough machining. Carbide tool Cemented carbide is composed of tungsten carbide (WC), titanium carbide (TiC), tantalum carbide (TaC) and 5% - 10% cobalt. Its hardness is much higher than that of high-speed steel. The maximum allowable working temperature can reach 1000 ℃. It has excellent wear resistance. When processing steel materials, it can reduce the adhesion between chips.
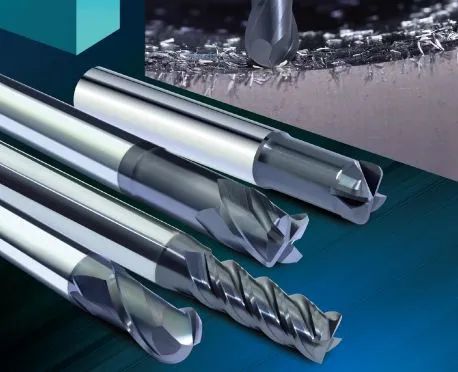
Carbide tools have good red hardness, when processing ordinary materials, generally dry cutting is adopted without cutting fluid. 1. During dry cutting, the temperature rise of the workpiece is high, which makes the workpiece prone to thermal deformation and affects the machining accuracy of the workpiece. Therefore, when selecting the cutting fluid, the sensitivity of cemented carbide to sudden heat should be considered, and the tool should be heated evenly as far as possible, otherwise it will lead to edge collapse. 2. For high-speed cutting, spray the cutting area with a large flow of cutting fluid to avoid edge collapse due to uneven heating of the tool, and reduce oil smoke pollution caused by evaporation due to excessive temperature. Ceramic cutter This material is made of aluminum oxide, metal and carbide sintered at high temperature. Its high-temperature wear resistance is better than that of cemented carbide, so dry cutting is generally adopted.
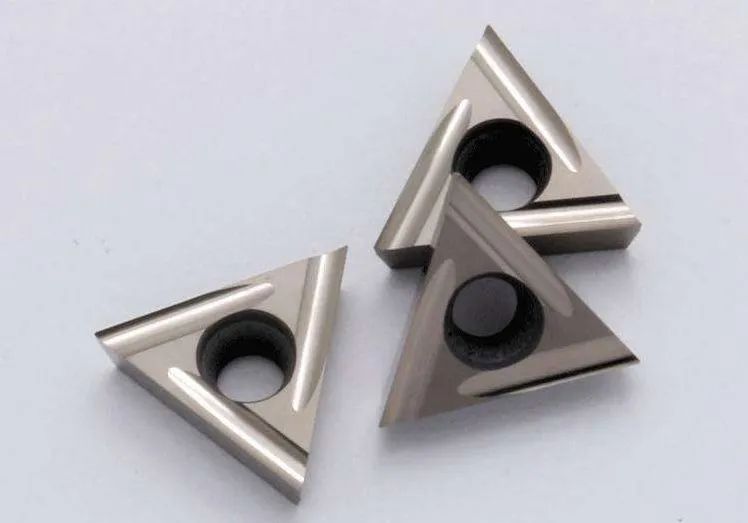
In consideration of uniform cooling and avoiding excessive temperature, water-based cutting fluid is often used, but it is better to pour continuously and fully without interruption. Diamond cutter Diamond tools have extremely high hardness, and generally use dry cutting. In order to avoid excessive temperature, water-based cutting fluid is also used in many cases, like ceramic materials.
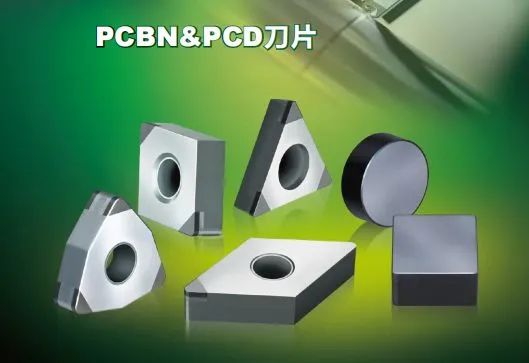
Selecting cutting fluid reasonably according to different tool materials can not only improve the surface quality and machining accuracy of the workpiece, but also reduce the thermal deformation of the workpiece and the wear of the tool, improve the durability of the tool and reduce the production cost. It is not easy to find a cutting fluid that can fit the tool exactly.