Cutting fluid stinks, rust solution!
May 19, 2022
Summer is here and the weather is heating up gradually. Are you still worried about the odor and rust of the cutting fluid? The following application technology introduces the main reasons for the odor and rust of cutting fluid, suggested measures, use and deployment and precautions.
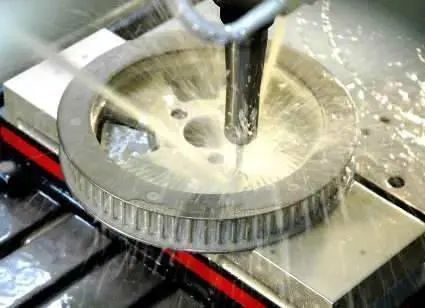
1. Common problems, causes and solutions. Machine or workpiece is rusted Main reasons: 1. Insufficient working fluid concentration Suggested measures: 1. Regularly measure the viscosity of the cutting fluid and maintain an appropriate concentration The main reason: 2. The pH value is reduced Suggested measures: 2. Supplement alkali substances to maintain pH value around 9 The main reason: 3. The rust inhibitor is consumed too much Suggested measures: 3. Supplement rust inhibitor Main reasons: 4. Deterioration and corruption of cutting fluid Suggested measures: 4. Replace with new fluid when it is seriously deteriorated Main reasons: 5. Long-term contact of dissimilar metals Suggested measures: 5. Avoid prolonged contact with dissimilar materials in the presence of cutting fluid Rust during stops between processes Main reasons: 1. The residence time between processes is too long Suggested measures: 1. Shorten the residence time between processes or apply anti-rust oil Main reasons: 2. The temperature difference between day and night is large, and the moisture in the air condenses Suggested measures: 2. Apply anti-rust oil Main reasons: 3. Corrosion by surrounding acid gas Suggested measures: 3. Apply anti-rust oil Main reasons: 4. Placed under abnormal climatic conditions such as typhoons and plum rains Suggested measures: 4. Apply anti-rust oil Rotten smell The main reasons: 1. The management of anticorrosion of cutting fluid is not in place Suggested measures: 1. Strengthen PH value and concentration management, maintain normal use value Main reasons: 2. Oil leakage, excessive mixing of chips Suggested measures: 2. Keep the cutting fluid clean, do not let it come into contact with food, tobacco, etc., and remove oil slicks and chips in time Main reasons: 3. The cutting fluid does not flow for a long time Suggested measures: 3. Regularly add antiseptic fungicides, and blow as usual on holidays Main reasons: 4. Inadequate anti-corrosion management Suggested measures: 4. Regularly measure the concentration and PH value of cutting fluid 2. Use and configuration 1) Add a certain amount of water to a clean container (such as a bucket); 2) Calculate the required amount of cutting fluid according to the required concentration according to the amount of water added; 3) Slowly add cutting fluid into the water, and stir well until the cutting fluid is completely uniform; 4) Add the prepared cutting fluid diluent into the machine tool, start the circulating pump, and circulate thoroughly. 3. Matters needing attention 1) Be sure to use a clean container to prepare the cutting fluid dilution; 2) Be sure to pour the cutting fluid into the water slowly, not the other way around; 3) Before changing the liquid, it is necessary to thoroughly clean and disinfect the equipment and pipelines to prevent the new liquid from being polluted and quickly corrupted; 4) A certain liquid level should be guaranteed in the liquid tank to avoid the increase of foam during use; 5) Ensure that the appearance, smell, concentration and PH value of the cutting fluid in use are detected every day; 6) If the machine tool is not in use, it must be ensured that it is cycled for 2-3 hours every day to avoid the generation of anaerobic bacteria; 7) It is recommended to clean the oil slick in the fluid tank 2-3 times a week and be sure not to litter the cutting fluid; 8) According to the usage of the cutting fluid, regularly clean and change the fluid. The longest use in winter is no more than 6 months, and it is best not to exceed 4 months in summer. Regular cleaning ensures the overall working environment. 4. How to monitor daily 1) Appearance: Daily inspection, color change, miscellaneous oil pollution, foam, foreign body intrusion, etc. 2) Odor: detected every day, aerobic bacteria: tasteless or sewage; anaerobic bacteria: rotten egg smell; fungi: musty smell or straw smell. 3) Concentration: Tested every day, controlled at +/-1%. 4) PH value: test every day, PH is controlled at 8.5-9.5. If the PH value is lower than 8.5, the lye should be replenished in time to avoid the rapid growth of bacteria, resulting in rusting of workpieces and machine tools, and odor of cutting fluid. Hope the above can help you.