Do you know the differences in quality control items in the production of oil-based cutting fluids and water-based cutting fluids?
September 06, 2021
Do you know the differences in quality control items in the production of oil-based cutting fluids and water-based cutting fluids? The main quality control indicators of oil-based cutting fluids (referred to as cutting oils) are: viscosity, flash point, pour point, fat content, sulfur content, chlorine content, copper corrosion, moisture, mechanical impurities, four-ball test, etc. Regarding the measurement method, please refer to the relevant test method standards, and only some items are briefly explained here. Fat content Fat is an oily additive in cutting oil, and an important indicator for classifying cutting oil. Fat in the cutting oil can reduce the coefficient of friction and reduce tool wear (especially effective in preventing the wear of the flank surface). The cutting oil with more fat is especially suitable for non-ferrous metal processing and occasions where the cutting volume is not large but the product precision and finish are high (such as precision turning screws). Generally, the saponification value can be used to roughly determine the fat content. If the fat content in cutting oil is too high or its quality control is improper, it is easy to form sticky substances on the machine and cause the machine parts to move inflexibly. In severe cases, it will become a paint film, the so-called "wearing yellow robe". Chlorine content Chlorine in cutting oil mainly comes from extreme pressure agents containing chlorine. Chlorine needs to be at a higher content (greater than 1%) in order to show an effective extreme pressure effect. If the chlorine content is less than 1%, it can be considered that it is not for improving lubricity. Generally, the chlorine content of extreme pressure cutting oil containing chlorine is above 4%, and the maximum content can reach 30% to 40%. However, due to occupational hygiene and environmental protection considerations, some countries have set the maximum content of chlorine in cutting oil. For example, Japan's JIS stipulates that the chlorine content should not exceed 15%. Chlorine is very effective in the processing of stainless steel as well as in the drawing and forming process. The disadvantage is that it is not stable enough, and will decompose to produce HCl when exposed to water or high temperature, causing corrosion and rust. Sulfur content Sulfur in cutting oil comes from two sources. One is the added sulfur-containing extreme pressure agent, and the other is from other sulfur-containing compounds that have no extreme pressure effect, such as the original natural sulfides in the Base Oil, rust inhibitors, and antioxidants. Effective sulfur only needs a very low content (0.1%) to produce a significant extreme pressure effect. Sulfur-containing extreme pressure agents are particularly effective in suppressing built-up tumors, but unfortunately, there is no simple way to detect sulfur with extreme pressure and sulfur without extreme pressure. Therefore, it is difficult to judge its extreme pressure only based on its sulfur content (especially when the sulfur content is not high). However, most cutting fluid manufacturers now indicate the sulfur content of the extreme pressure agent added in their product manuals. Copper sheet corrosion The method of measurement is the copper sheet method. The magnitude of corrosion activity is represented by the number of stages, with 1 to 2 levels being low activity or inactive, and 3 to 4 levels being high activity. The larger the number, the stronger the corrosion activity. Copper is very sensitive to sulfur. This method can be used to determine whether there is a sulfur-containing extreme pressure agent in the cutting oil and the activity of the extreme pressure agent (note: this method cannot determine the amount of sulfur-containing agent). This item is also an important indicator of the classification of cutting oil. Four ball test Can measure the maximum non-stick bite load. With this method, the extreme pressure of cutting oil can be roughly judged, especially when combined with sulfur, chlorine content and copper corrosion, it can have a more comprehensive understanding of its lubricity. However, it should be emphasized that the extreme pressure given by the four-ball test is only the evaluation result under standard conditions, and there is no strict correspondence between this result and the cutting performance.
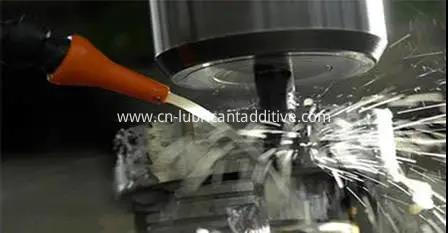
Water-based cutting fluids must be diluted with water during application, and the test items can also be divided into two parts: direct measurement and water-added measurement. Directly determined items include: storage stability, sulfur and chlorine content, non-volatile components, etc. The items to be measured after adding water include surface tension, pH value, foaming, rust resistance, corrosiveness, adaptability to paint, allowable amount of salt, and antibacterial properties. The meaning of most of these items is relatively clear, and the following is only a description of individual items. Storage stability Although the concentrate of water-based cutting fluid is a homogeneous liquid in appearance, it is actually mostly a colloidal system and contains a lot of water. After long-term storage and temperature fluctuations, if the formula is improper, it is easy to cause precipitation, delamination and other phenomena and often cannot be restored. So this is a very important test item. Non-volatile components The water-based cutting fluid concentrate contains water. This item is used to determine the content of its effective components. Allowable amount of salt This test is used to understand whether the cutting fluid allows the use of tap water with higher chlorine content to prepare working fluids. Surface Tension In most cases, the liquid with low surface tension is easy to spread on the solid surface. Therefore, a considerable number of people regard the surface tension as a measure of the permeability of the cutting fluid. But strictly speaking, there is no direct correspondence between the two. Permeability is a rather ambiguous concept, which seems to be more closely related to wettability and fluidity (viscosity). Surface tension can be used as an indicator for judging whether a surfactant is added to the cutting fluid. Because a small amount of surfactant can greatly reduce the surface tension of water. In addition, the surface tension is not as small as possible. Too small surface tension sometimes brings other negative effects. Antibacterial test Water-based liquids, especially emulsions, are prone to bacteria and spoilage, so the antibacterial ability is an important performance index. However, it has not attracted much attention in our country in the past, and it has not been adopted as a quality index for water-based liquids. There are already some simple measurement methods abroad, and qualified units should apply them as much as possible.