How to mix metal coolant?
October 22, 2022
The water-based metal coolant must be properly mixed and kept in a reasonable concentration range to maximize performance. When the concentrated liquid and water of the coolant are mixed and filled into the liquid storage tank and the central system of the machine tool, the concentration of the coolant must be tested to ensure that the initial concentration is correct. The concentration can be measured with a chemical refractometer and a concentration tester. The concentration can be expressed either as a percentage or as a ratio of the volume of the metal coolant concentrate to the total mixture.
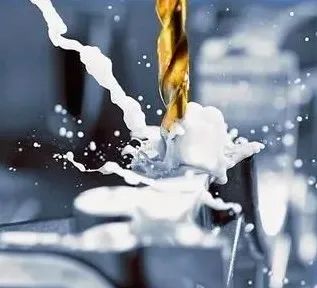
How to mix metal coolant? When mixing the coolant, add the emulsion to the water. The emulsifier will suspend the oil droplets in the water and produce stable and diluted emulsion as expected. If water is added to the concentrate in reverse order, the emulsifier will release part of the concentrate to capture water molecules. In this way, a reverse emulsion will be generated, which will lead to the loss of some components in the coolant, such as lubricating components, bactericides and corrosion inhibitors. Some or all of the chemical components in the coolant may be affected. The stability and concentration of mixing will also be affected by the reverse emulsion. After mixing the coolant, the refractometer shall be used to test its concentration to see if it meets the requirements for use. For example, a 100 gallon liquid tank has only 90 gallons of metal coolant left after a whole day's work, of which 10 gallons are consumed due to evaporation, loss and splash, that is, 10% of the tank volume. The daily consumption of metal coolant varies, depending on the operation, the type of metal coolant itself, the number of workpieces processed, and other workshop production conditions. It should be known that the coolant contains certain components that will have specific effects. These may include: Fungicide: Prevent the growth of certain bacteria and molds that produce odor. Corrosion Inhibitor: to prevent rust or corrosion of metal scraps in machine tools, machine tool parts and liquid tanks. Lubricant: improve tool life and productivity Foam inhibitor: to prevent foam problems. These components are also consumed after performing their respective functions and need to be compensated every day. Example: When processing cast iron, the coolant needs to contain a large amount of corrosion inhibitors (rust inhibitors). Corrosion inhibitors prevent rust of metal chips accumulated in machine tools, machined workpieces and fluid tanks. Because cast iron has a large surface area that needs to be protected, the processing process will deplete the corrosion inhibitor components in the coolant at a rate greater than the consumption of lubricant components. This is called "selective consumption". The way to deal with selective consumption is to supplement the coolant mixture every day. The following operations are examples of selective consumption: Cast iron: fast consumption of corrosion inhibitor (rust inhibitor). Aluminum: consumes lubricant components, but generally does not affect corrosion inhibitor components. Dirt/oil sump: consumption of germicide ingredients. High pressure/high speed operation: consumption of defoaming ingredients. Hard water: consumption of emulsifier components that maintain the coolant as a whole. The correct procedure to replenish the coolant volume and maintain the correct coolant concentration is to fill the reservoir with pre prepared coolant every day. The mixing concentration is slightly lower than the mixing concentration of the liquid that first fills the central system or the machine tool reservoir. Do not add water alone. Normal recommended supplement concentration (final target concentration is 5%) Emulsion: daily supplement concentration shall be 3% - 4%. Semi synthetic coolant: daily supplement concentration shall be 2% - 3%. Fully synthetic coolant: the daily supplement concentration shall be 1% - 2%. The values listed above are for reference only, and the actual make-up concentration may vary depending on the specific processing, workpiece configuration, coolant type, water quality, environmental conditions, filtering system and other factors. Even if properly supplemented, with the aging of the coolant, other additives (such as bactericide ingredients) may be required to extend the service life of the coolant and maintain the performance of the coolant. What happens if the metal coolant concentration is too high? If the concentration of metal coolant is higher than the recommended concentration, measures must be taken to reduce its concentration. The higher the concentration is, the more problems will arise, just as the lower the concentration is, the more problems will arise. We do not recommend simply adding water to try to solve the problem of excessive concentration. Just adding water may lead to too little content of key components, which is very likely to cause problems such as corrosion, bacteria breeding, tool life shortening, emulsion losing homogeneity, etc. The best way to solve the high concentration of coolant is to empty part of the coolant into the barrel or other accommodating area, and then replace this part of the volume with a premixed mixture from a lower concentration. This will reduce the concentration of the coolant and maintain the required workability. Please remember that maintaining the concentration range of metal coolant according to the recommendations will improve the overall performance of the operation, increase productivity, extend the service life of the coolant, reduce the cost of waste liquid treatment, and improve the overall comfort of the operator. We suggest that the coolant should be mixed reasonably at the beginning of the work, which is very important. Routine concentration check and correct replenishment are the key to coolant management.