In this way to identify the cutting fluid, save at least 10% cost
June 13, 2022
As an important supporting material for metal cutting processing, the application of water and oil in metal cutting is accompanied by the emergence of water and oil in metal cutting processing. With the appearance of various machine tools, the cutting fluid has also begun to apply large -scale applications. The cutting fluid is currently mainly used in large enterprises such as the automotive industry, mold processing industry, and mechanical manufacturing industry, which mainly plays the role of lubrication and cooling. The correct use of the cutting fluid is to effectively exclude the chip, which also helps the extension of the life of the tool. If the nozzle of the cutting liquid is appropriately placed, the crumbs of the milling cutter and the drill head are blocked by the crumbs or the dumps are not smooth.
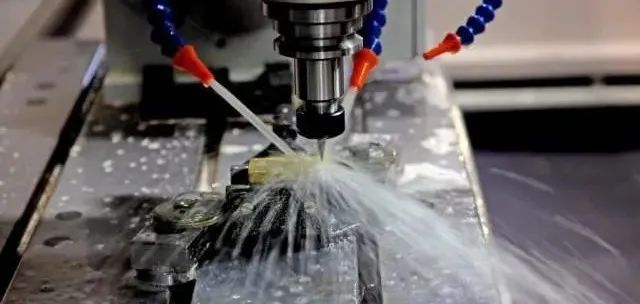
Let's talk briefly below. Even if we are in the factory, we can use the simplest methods to compare the main performance indicators of different cutting fluid products. 1. Cutting fluid performance The longer the life of the knife and the better the processing surface of the processing, the better the cutting lubrication performance. In the case of the same equipment, the same tool, and processing the same workpiece, compare the life of the knife (the number of parts or cutting distances that can be processed by the knife) and the processing quality (surface smoothness). Lubrication performance is a very important indicator of cutting fluid. It directly affects the quality and cost of processing. But it cannot be judged intuitively because you cannot know how much the formula of the cutting fluid and its effective lubrication ingredients. 2. Stability The following two items have any layers, impurities and uneven phenomena. You can determine that the stability of the cutting fluid is poor. Take an appropriate amount of the original solution and place it in the transparent container for 24 hours to observe whether the original liquid has layers and impurities, and whether it is uniform; Take an appropriate amount of primary solution and make 5%diluted solution with tap water, and set up for 15 minutes in a transparent container to observe whether the diluted solution is uniform and whether there are layers and impurities. 3. Elimination nature The experimental foam can disappear within 15 seconds, the foam performance is qualified, the faster the foam, the better. Configure the 5%concentration dilution and place it in a transparent reagent bottle to cover the lid. Then use the normal force to shake up and down the reagent bottle for 15 seconds, and then stand on the desktop and start timing and observe: If the foam generated in the bottle can disappear within 15 seconds, the foam performance is qualified. 4. Prevent rust and corrosion The later the rust appears, the stronger the natural anti -rust and anti -corrosion capacity. Configure 5%concentration diluted liquid, select the moderate processing parts (processed by cutting processing) in the cutting solution (half an hour to a few hours. According to the length of the part processing time), take it out and quiet in the air. Observation will rust or corrode parts after 3-5 days. In particular, this method can only be judged initially in this method. For some special materials (such as aviation aluminum alloy), more stringent laboratory verification is often required. 5. Antibacterial ability The earlier the smell, the worse its antibacterial ability. Configure 5%concentration dilution liquid and static in the container, and regularly smell the change of the smell of the cutting solution. This item is directly related to the life of the cutting fluid. The principle of inhibitory bacteria in most products depends on the sterilizers in the product formula. Only a small amount of products use biological bacteriostatic methods. 6. Anti-hybrid ability Observe the change of the dividing line: The cutting fluid with a weak anti -oil oil capacity will soon be mixed with the oil to make the dividing line more and more blurred. Configure 5%concentration diluted liquid and place it in a transparent container, and then add an appropriate amount of hydraulic oil or guide or rail oil in the cutting solution. The oil will float on the surface of the cutting solution, and the oil and water will have a clear boundary. 7. Whether it contains nitrite Use a special nitrite to detect test paper. Or the manufacturer is required to provide MSDS files. If the test strip becomes red, 99%can determine that it contains carcinogenic nitrite. The deeper the redness, the higher the content. 8. Consumption of the cutting fluid Two reagent bottles can be used to prepare the same concentration dilution solution and maintain the same capacity. Then take two exactly the same standard samples (such as two long steel rods), use the same method to immerse the sample into the cutting fluid in the reagent bottle and remove it (the cutting fluid will be adhered to the sample and drip it outside outside To. After repeating the same number of times the same times, the amount of the remaining cutting fluid in the comparative reagent bottle. The leftovers are not easy to be consumed by parts and dandruff. Take away products with high consumption will bring high cost. In addition, if you want to compare the cooling performance of the cutting fluid, there is still a simple method. However, as long as it is a water -soluble product, the cooling performance is not much different. There are also requirements for settlement for full synthetic grinding fluid. That is, the ability of milling and metal particles to quickly settle in the grinding solution. This can intuitively observe changes in the degree of transparency of the grinding fluid. Products with better settlement can maintain good transparency for a long time.