Several issues that must be mastered in making turbine oil!
October 01, 2022
1. What is the basis for determining the speed regulating oil pressure and lubricating oil pressure of the steam turbine? The regulating system of the steam turbine usually uses oil to transmit the signal and act as the power to make the oil motor act, opening and closing the regulating valve and the main valve. In order to ensure quick and sensitive adjustment, it is necessary to maintain a certain speed regulating oil pressure. The commonly used speed regulating oil pressures of steam turbines are 0.4 ~ 0.5MPa, 1.2 ~ 1.4MPa, 1.8 ~ 2.0MPa and so on. Generally speaking, high oil pressure can make the adjustment system more sensitive, and the size of the oil engine and the wrong throttle structure can be reduced. Some of the speed regulating oil pressure is as high as 4.0MPa. But when the oil pressure is too high, it is easy to leak oil and catch fire. The lubricating oil pressure of the steam turbine is calculated during the design according to the weight of the rotor, the rotational speed, the structure of the bearing bush and the viscosity of the lubricating oil, so as to ensure that a good oil film can be formed between the journal and the bearing bush, and there is enough oil for cooling. Therefore, the steam turbine lubricating oil pressure is generally 0.12 to 0.15 MPa. Excessive lubricating oil pressure may cause oil leakage from the oil block and vibration of the bearing. If the oil pressure is too low, the oil film will not be well established, and even the oil will be cut off and the bearing bush will be damaged.
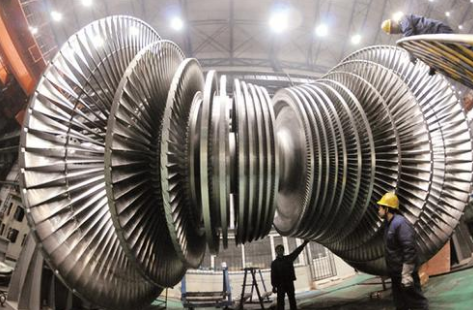
2. Why should a range hood be installed in the turbine oil tank? The function of installing a range hood in the fuel tank is to remove the gas and water vapor in the fuel tank. In this way, on the one hand, the water vapor does not condense in the oil tank; on the other hand, the pressure in the oil tank is not higher than the atmospheric pressure, so that the bearing return oil smoothly flows into the oil tank. On the contrary, if the oil tank is closed, a large amount of gas and water vapor will accumulate in the oil tank to generate positive pressure, which will affect the oil return of the bearing, and at the same time, it is easy to accumulate water in the oil tank. The range hood also has the function of removing harmful gases so that the oil quality is not easy to deteriorate. 3. Why should a drain pipe be installed at the bottom of the fuel tank? During the operation of the steam turbine, due to the large leakage of steam from the shaft seal, the poor drainage of the steam-driven oil pump, and the excessive leakage of water from the inlet flange of the water-cooled generator rotor, the steam turbine oil contains water. After the oil with moisture returns to the fuel tank, because of the large proportion of water, the water and the oil are separated and deposited at the bottom of the fuel tank. Timely removal of this water can prevent the water that has been separated from being mixed with the oil and deteriorating the oil quality. So there is a drain pipe at the bottom of the tank. 4. What is the harm of the deterioration of turbine oil quality? The quality of turbine oil is closely related to the normal operation of the turbine. The deterioration of the oil quality changes the performance of the lubricating oil and the oil film force, causing the lubricating parts to not be well lubricated, and as a result, the bearing bush is melted and damaged. Serious consequences of device failure. Therefore, attention must be paid to the supervision of the quality of turbine oil. 5. What are the quality indicators of turbine oil? The quality of turbine oil has many indicators, mainly including five indicators such as viscosity, acid value, acid-base reaction, degree of demulsibility and flash point. In addition, transparency, freezing point temperature and mechanical impurities are also criteria for judging oil quality. 6. What is the viscosity of turbine oil? What is the viscosity index? Viscosity is the criterion for judging the dilution of turbine oil. If the viscosity is high, the oil will be thick and not easy to flow; if the viscosity is small, the oil will be thin and easy to flow. Viscosity is measured in Enn's degree, and the commonly used viscosity of turbine oil is Enn's degree of 2.9 to 4.3. Viscosity has a great influence on the lubricating performance of the bearing. If the viscosity is too large, the bearing will easily heat up, and if the viscosity is too small, the oil film will be damaged. As the oil quality deteriorates, the viscosity of the oil increases. 7. What is the acid value of turbine oil? What is an acid-base reaction? The acid value indicates how much acid is in the oil. It is calculated by how many milligrams of potassium hydroxide per gram of oil are needed to neutralize. The acid value of the new turbine oil should be no more than 0.04KOHmg/g oil. When the oil quality deteriorates, the acid value rises rapidly. Acid-base reaction refers to whether the oil is acidic or basic. A good turbine oil should be neutral. 8. What is the degree of demulsibility? What is a flash point? The degree of demulsibility is the ability of oil to quickly separate from water, and it is expressed in terms of the time required for separation. A good turbine oil has an anti-emulsification degree of not more than 8 minutes. When the oil contains organic acids, the anti-emulsification degree will deteriorate and increase. Flash point means that when the turbine oil is heated to a certain level, part of the oil turns into gas, which can be burned with a little fire. This temperature is called the flash point (also known as the ignition point). The temperature of the steam turbine is very high, so the flash point should not be too low. Good The flash point of the turbine oil should not be lower than 180℃. As the oil quality deteriorates, the flash point decreases. 9. Why must vent holes and vent pipes be installed on the steam turbine bearing cover? Generally, the bearing is in a state of negative pressure, which is usually caused by the suction of the oil flowing out of the bearing. Due to the negative pressure formed in the bearing, steam is sucked into the bearing and water droplets are condensed. In order to avoid negative pressure in the bearing, vent holes or vent pipes are provided on the bearing cover to communicate with the atmosphere. On the other hand, the vent pipe provided on the bearing cover can also play the role of removing the flue gas generated by the steam turbine oil in the bearing due to the heating, so that the pressure in the wheel bearing box is not higher than the atmospheric pressure. During operation, attention should be paid to keeping the ventilation holes unobstructed to prevent clogging. The vent hole of the front bearing cover of a steam turbine of a factory was blocked, and the bearing box accumulated flammable gas, which was detonated by the electric spark in the bearing box, resulting in an explosion accident of the front bearing box. 10. What determines the capacity of the main fuel tank? What is the cycle rate of turbine oil? The oil storage capacity of the main oil tank of the steam turbine depends on the size of the oil system, which should meet the oil consumption of the lubrication and adjustment system. The larger the unit, the more oil used in the adjustment and lubrication system. The capacity of the fuel tank is also larger. The circulation rate of the turbine oil is equal to the ratio of the oil output of the main oil pump to the total oil volume of the fuel tank per hour, which should generally be less than 12. If the cycle ratio is too large, the turbine oil stays in the fuel tank for a short time, and the air and water cannot be separated in time, resulting in the rapid deterioration of the oil quality and shortening the service life of the oil.