Summary of rolling oil use problems and solutions
November 16, 2022
During the use of rolling oil emulsion, with the change of temperature, high-pressure nozzle shearing, continuous circulation and other factors, the distribution of oil particle size in the emulsion is affected, and various problems occur. Here are the corresponding solutions to some problems in the use of rolling oil!
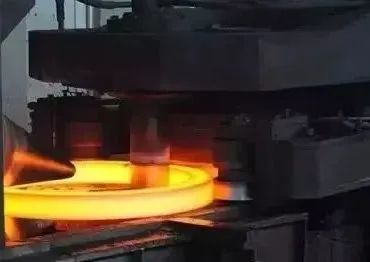
1. Scratches: mainly caused by insufficient lubrication 1) High speed steel rolling produces a lot of deformation heat due to large reduction, the temperature of the roll and the steel plate increases, the oil film thickness between the roll and the steel plate becomes thinner and the amount of oil film becomes smaller when the amount of emulsion spraying is insufficient, and the direct contact between the roll and the steel plate causes thermal scratches; 2) If thermal scratch occurs under good rolling conditions, the strength of rolling oil film may be insufficient; 3) The rolling speed is too high, the reduction rate is too large, and the material hardness is too large. The speed can be reduced appropriately and the rolling process can be adjusted Solutions: 1) Increase emulsion temperature 2) Increase emulsion concentration 3) Increase the emulsion injection amount (for the surface of upper and lower rollers) 4) Change the roll roughness (reduce) 2. Slip phenomenon Slip is the opposite of thermal scratch. As the oil film thickness between the steel plate and the roll is too large or the range of fluid lubrication is increased, the friction coefficient decreases. When the friction coefficient decreases to a certain value, slip will occur. The deep slip scar can only be solved by changing the roll. Pay attention to the median value of rolling production. Solutions: Reduce the concentration, temperature and iron powder content (skimming and magnetic filtration) to change the roller roughness (increase) 3. Rolling force rise When the reduction of rolled very thin plates is too large or the hardness of rolled steel plates is too large, the rolling force is very easy to rise. Of course, it is necessary to consider the reduction rate and the distribution of tension, because tension can change the deformation resistance of metal. In addition, lubrication can also be used: because lubrication can change the stress state of the denatured area, making the rolling deformation easier. Solutions: The temperature and concentration of emulsion shall be appropriately increased to increase the adhesion of emulsion on the surface of steel plate, enhance lubrication, increase the reaction capacity of oiliness agent extreme pressure agent, reduce the deformation resistance of steel plate, and improve the thermal expansion degree of roll to reduce the rolling force; Reduce the roughness of the roll, reduce the friction coefficient and reduce the rolling load; Check whether there are a lot of impurities such as foreign oil in the emulsion; Leakage of cooler and heater; Enter alkaline substances or tap water (discharge part or all of them). 4. Blackening of rolled steel plate 1) Emulsion temperature is too high or too low 2) The emulsion concentration is too low or the rolling force is large 3) The raw material is defective or the pickling is not clean 4) Excessive iron powder in emulsion 5) Improvement of roll roughness (reduction of roughness) 6) Check whether there is foreign oil flowing in (even if the drain is cleared) 5. Rust or stain (milk stain) on rolled steel plate 1) The biggest reason is that lotion and water are not removed during rolling 2) High humidity around the rolling mill 3) The steel plate is not cleaned or rusted after pickling 4) Improve the oxidation resistance of oil Solutions: a. Check that the chloride ion on the steel plate surface of the pickling section and drying equipment is too high; b. The rolled steel plate shall be effectively squeezed or purged with compressed air (check the pressure and dryness of the squeeze roll and compressed air); c. Properly increase the temperature of emulsion, steel plate and water evaporation; d. Ensure the liquid level is normal, do not roll steel with low liquid level, and skim oil regularly. 6. Vibration phenomenon: During the vibration, the thickness of the steel plate fluctuates and the tension fluctuates, which is easy to cause belt breakage: 1) The manufacturing speed is too high, and the thickness of the finished product is thin, the pressure is low, and the deformation is small 2) The tension before strip steel may be large 3) The lubrication may be too good or too bad 4) The roughness of the work roll may not be enough 5) Backup roll and intermediate roll may be damaged 6) The gap between the roller bearing and the bearing seat may be large 7) The clearance of discharge window may be large