The most scientific and practical metal processing waste liquid emission reduction measures!
October 04, 2021
The most scientific and practical metal processing waste liquid emission reduction measures! Based on the analysis of the advantages and disadvantages of various metal processing fluid emission reduction methods, this paper proposes more scientific and practical emission reduction technologies to reduce the production of waste liquid from metal processing enterprises, and fundamentally help metal processing users to achieve emission reduction.
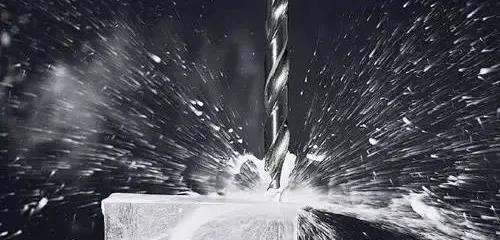
For machine tool processing enterprises, the amount of cutting fluid is huge, the waste liquid after machining contains a lot of harmful components and cannot be directly discharged. The cost of sending it to a third-party treatment company is expensive, and the capital investment of self-built sewage treatment equipment for the first time is also high. Therefore, reducing the discharge of waste liquid is an important and fundamental choice for machine tool processing enterprises. In order to reduce emissions, reduce environmental pressure and waste liquid discharge costs of metal processing companies, companies in all links of the industry's value chain are making unremitting efforts. At present, the actual emission reduction methods are mainly as follows: Dry processing 1. Micro spray lubrication 2. Scientific maintenance, prolong the service life of processing fluid 3. Environmentally friendly products with new antibacterial technology 4. Two-phase control technology 5. Compatible technology Dry cutting Dry cutting refers to a processing method that does not use media, but uses cold air guns, compressed carbon dioxide, and liquid nitrogen to cool the surface of parts. The success of dry cutting depends on the selection of parts materials, tool materials and tool coatings. Dry machining has been used for many years in the field of cast iron and aluminum processing. But on the other hand, the current huge shortcomings of this method are: the chips cannot be transferred out of the cutting area and the machine tool, as well as the smoke and dust generated.
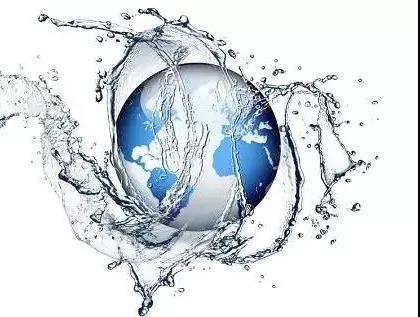
Micro spray lubrication In this cooling method, the cooling liquid is sprayed through the system at one time (non-recycling use), so maintenance is greatly reduced, and the use of metalworking fluid is also drastically reduced, achieving the goal of drastically reducing emissions. This method has been widely used in crankshaft machining applications in Europe and Japan. The disadvantage of this method is that the chips cannot be transferred. The compressed air takes the chips out of the cutting area, but cannot take the chips out of the machine. In addition, this method needs to generate oily aerosol, which usually requires modification of existing equipment and coordination. New spindle design; moreover, some processes cannot be applied at present, such as grinding. Scientific maintenance, prolong service life This is currently one of the most effective and economical ways to reduce costs and reduce emissions in the use of machine tools. This method adopts an effective filtration system; effectively monitors the fluid in use and performs preventive maintenance; and uses a centralized fluid supply system for mass-produced parts as much as possible. The specific methods are: daily detection and maintenance of the concentration and pH value; the use of a mixer to mix the liquid to ensure the emulsification effect of the liquid; the daily addition to maintain the normal concentration; the concentrated sedimentation, centrifugation, oil skimming and After filtration, it is added as a daily additive to other fluid systems in use; daily oil skimming is performed on all systems, and slag is removed regularly. In order to achieve the above-mentioned effective maintenance and ultimately achieve the purpose of extending the service life of the processing fluid, the executive team has put forward very high requirements, and Business Opportunity Court provides enterprises with [Industrial Maintenance and Chemical Management Training] 2022 3 Classes will be held in Suzhou from December 25th to 27th. Through dedicated and effective management, every year, we will make due contributions to the cost reduction and emission reduction of these enterprises. New antibacterial technology Environmentally friendly products using new antibacterial technology: For customers who currently use cutting fluids with a short life, this is the most suitable and effective way to reduce emissions. Using this type of cutting fluid can greatly extend the use time, thereby directly reducing fluid replacement and Discharge of waste liquid. Use advanced antibacterial technology to prevent bacteria from reproducing, and use highly refined base oils and additives to reduce the impact of impurities in the raw materials on the human body and the environment. These products have the characteristics of high lubrication and long life. Generally, the life of a single machine is one to two years, and the life of a centralized system is 3-5 years, or even 5-10 years. Two-phase control technology The use of two-phase control technology can reduce the amount of coolant used as much as possible. Two-phase control technology uses two separate combination agents, the oil phase or the water phase are controlled separately, each is a separate product, and both are added at the same time when used, but only any consumed phase is added separately when adding. The oil phase in the two phases is mainly lubricating additives and emulsifiers, which provide cutting lubricity during use, ensuring the stability of the emulsion and the cleaning ability of the product; while the water phase is mainly composed of biologically stable additives and anti-rust inhibitors. It can protect the product against microbial growth, prevent rust and maintain the pH of the product. Compatible technology Compatible technology, that is, using the same chemical technology for oil and liquid that may leak into the processing fluid. For example, systems that do not contain mineral oil are used, such as hydraulic oil, guideway oil, cutting oil, and cutting fluid. The oils are all vegetable oil base oils to improve compatibility between products; reduce the impact of pollution on the coolant. The cleaning agent washed with the cutting fluid can be recycled into the cutting fluid as a water phase supplement, and equipment leakage such as rail oil, hydraulic oil, etc. can be used as the oil phase supplement, so as to directly reduce the discharge of waste liquid and reduce the original coolant liquid Add to. In systems that use cutting oil, you can also consider the use of multifunctional oils, such as the use of hydraulic oil, cutting oil, and Gear Oil to reduce the impact of equipment oil leakage on cutting oil. The effect of each emission reduction technology introduced above is closely related to the size, consumption, processing technology and material of the customer, but I believe that it will help you to develop ideas in terms of reducing the production of waste liquid, reducing the cost of use and emission. The concerted efforts of local governments and enterprises in the industrial chain will definitely improve our environment and return us to a beautiful home.