The mysterious "protective umbrella" of metalworking fluids
January 05, 2022
Metalworking fluid is an indispensable and important supporting material for machining. It can improve machining accuracy and reduce tool wear. Choosing the right processing fluid makes many complicated processing possible. However, the hazards of processing fluid to human health and safety cannot be ignored. People are paying attention to its hazards, and research work in this area is also being carried out. Metalworking fluid calls for environmental protection and health.
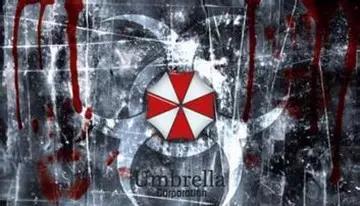
As far as metalworking fluids are concerned, the additives used are undergoing many changes, because customers want high-performance and environmentally friendly products. Many companies attach importance to the possible health problems of employees in the production department. Whether they can provide environmentally friendly, healthy and safe products that are universally applicable to the world is a challenge facing all metal processing companies. We found that the current market demand for metalworking fluids with low odor, no skin irritation, low sensitivity and no formaldehyde substances is increasing. Metalworking fluid users usually hope to reduce the microbial content through other safer and environmentally friendly technologies, thereby extending the service life, which has brought huge challenges to the entire industry. Regulatory restrictions on processing fluid additives Metal processing companies are looking for safer and more environmentally friendly metal processing fluids, and the same is true for regulatory agencies. Regulatory agencies in many regions have formulated relevant operating guidelines specifically for how to label dangerous goods. This will require a clear mark of the specific non-environmentally safe ingredients used in metal processing fluids, so as to provide a safer working environment for metal processing companies. In many countries in Asia (such as China, Japan, and South Korea), paying attention to the safety and health of metalworking fluids is also becoming a trend. If a major country of use restricts the use of fungicides, it will cause all foreign suppliers to re-evaluate their product formulations to ensure that it is increasingly important to produce products that meet national standards. Even in regions or countries where there are no regulatory restrictions, many metalworking fluid companies prefer to use "formaldehyde-free" or "made from sustainable raw materials" as the selling point of their products, thereby enhancing the value of the entire brand. This also requires Additive suppliers provide them with more suitable products. Every customer and every industry is different. For example, some end users of metalworking fluids do not want to use metalworking fluids containing special amines (such as DCHA or other secondary amines), and some users may refuse to use metalworking fluids in order to provide employees with a better working environment. Use products that contain ethanolamine or have a pungent odor. Customized solutions for different industries Most companies follow the principle of "one formulation is not suitable for everyone" when producing metalworking fluids. Nowadays, it has become the biggest challenge to require formula products to be universally applicable to various operations and metal processing. Certain industries, such as the manufacturing process of aluminum parts for aerospace and automotive applications, require metalworking fluids not to adversely affect the appearance of the parts. This usually requires the alkali performance of the metalworking fluid to be stabilized at a low pH value ( 8.5-9.0). However, at such a low pH, it is often difficult to ensure anti-corrosion control. However, primary amine products can reduce the PH value and achieve anti-corrosion control at the same time, thus solving the thorny problem in this industry. In addition to providing various customized solutions for each industry, it is also necessary to provide metalworking fluids that can be applied in various regions. For example, the water quality that affects the service life of the liquid has a huge impact on the overall performance of these liquids. The calcium and magnesium cations in the water will react with the anionic liquid components (fatty acid salts, petroleum sulfonates, etc.), resulting in emulsion stability And corrosion control is reduced. Anions in water (such as chloride and sulfate) can also cause corrosion problems. Softened, deionized or reverse osmosis water (although usually has a positive effect on liquid performance and service life) will increase foam formation. Foam control is one of the most difficult problems for liquid manufacturers and users to solve, and due to higher processing speeds and smaller footprint, foam control has now become a more difficult problem. Responding to the challenges of GHS One of the main challenges we foresee at the moment is the Globally Harmonized System (GHS) for the classification and labeling of chemical hazards. A document developed by the United Nations (UN) in 2012 provides guidelines for chemical companies to classify their products. The guidelines require companies to affix labels related to health, physical and environmental hazards on chemicals and provide information related to the content of product labels. Although the global standard has the benefit of consistency, its implementation has become a challenge for the metalworking fluid industry. As mentioned earlier, more and more end users require metalworking fluids to be more beneficial to employee health and environmental safety. GHS aims to make assessment easier. The classification system is a standardized system composed of symbols, information words, hazard statements and precautionary statements on all product labels and safety data sheets to provide users with information related to dangerous goods.