Under the goal of "double carbon", an effective way to reduce the carbonization of metal cutting fluids
March 19, 2022
Metal cutting fluid By developing high-performance, easily degradable environmentally friendly cutting fluids, establishing cutting fluid management and maintenance systems, and recycling cutting fluid waste fluids, cutting fluids can play a better role in machining and reduce Tool wear, improve processing quality, and improve working environment; at the same time, it can also improve the biodegradation rate of cutting fluid, prolong the service life of cutting fluid, reduce waste fluid discharge, and reduce the impact of cutting fluid on human body and the environment, thereby helping the manufacturing industry. Green and low-carbon transformation, and promote the realization of the "double carbon" goal. 1. Develop high-performance, easily degradable, environmentally friendly metal cutting fluids At present, most of the cutting fluid developers choose mineral oil as the Base Oil, which consumes a lot of petroleum resources, but also has poor biodegradability, and the waste fluid is difficult to handle, causing a heavy environmental burden. In addition, there are many kinds of cutting fluid additives, some of which are harmful to the human body and the environment, such as the commonly used extreme pressure additive short-chain chlorinated paraffin, which is not easy to degrade and easily accumulates in living organisms, which can cause cancer, teratogenicity and death. Commonly used inorganic salt rust inhibitor sodium nitrite combined with organic alkali in cutting fluid can generate carcinogenic nitrosamines. The formaldehyde released by the commonly used formaldehyde-releasing fungicides in the environment is carcinogenic and teratogenic. Therefore, using biodegradable vegetable oil or vegetable oil-based synthetic ester to replace mineral oil as base oil, and using new non-toxic and harmless additives to replace traditional toxic and harmful additives, the development of high-performance, easily degradable environmentally friendly cutting fluid has become a industry trends. Compared with mineral oil-based commercial fluids, the biodegradation rate of vegetable oil-based titanium alloy cutting fluids is significantly better than that of mineral oil-based commercial fluids, which can effectively reduce the pressure of subsequent waste fluid treatment and reduce the impact on the environment. According to the above test results, vegetable oil-based cutting fluid has stronger lubricating performance and higher biodegradation rate than traditional mineral oil-based cutting fluid. By replacing the mineral oil in the cutting fluid with vegetable oil, not only the dependence on petroleum products is reduced, but also the cutting fluid has the effects of prolonging tool life, reducing tool wear and reducing pollution.
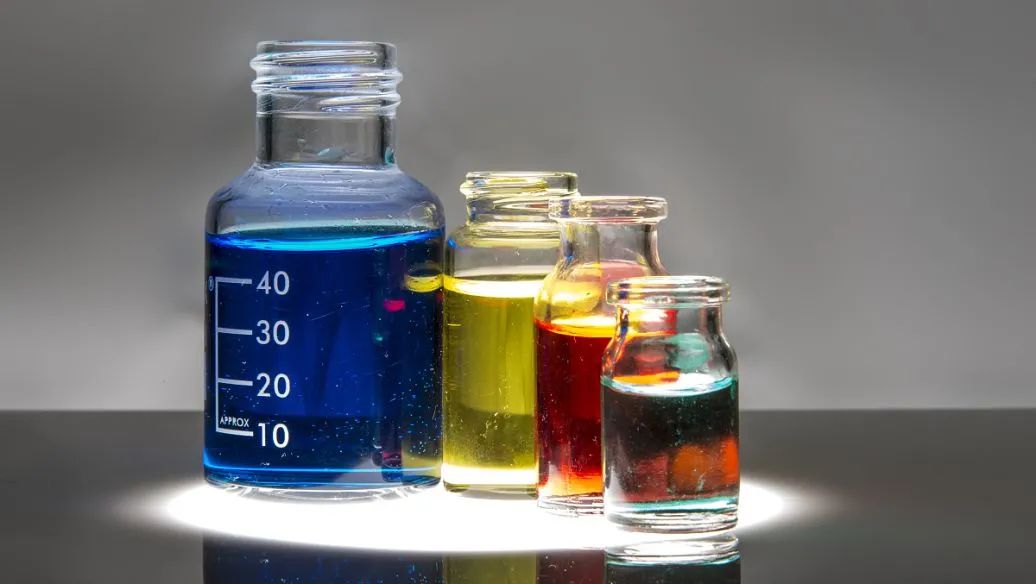
2. Establish metal cutting fluid management and maintenance system Even a cutting fluid with good performance, if used improperly and poorly maintained, will have many problems, such as rust, decreased lubricating ability, increased foam and shortened life. Therefore, in machining, users should not only choose high-performance environmentally friendly cutting fluids, but also master the correct use, management, and maintenance methods of cutting fluids in combination with on-site processes, so as to give full play to the role of cutting fluids and reduce machining. During the process, the wear of the tool is improved, the processing quality is improved, and the consumption and discharge of cutting fluid are reduced. However, for most enterprises, because metal cutting fluid technology involves many disciplines, management is difficult, there are many problems, and there is a lack of full-time personnel who are familiar with cutting fluid related knowledge. Therefore, based on the actual situation of users, it is particularly important to establish a systematic and complete cutting fluid management and maintenance system for improving the processing level of the manufacturing industry and reducing consumption and emission reduction. After choosing the appropriate cutting fluid, the original cutting fluid in the machine tool should be replaced before starting to use. step. After the replacement, in order to make the cutting fluid play a good role, it still needs to be maintained. In daily maintenance, the appearance, concentration, pH value, electrical conductivity, water hardness, foam, anti-rust performance and microbial colony count of the cutting fluid should generally be monitored. At the same time, it is also necessary to ensure the smooth circulation of the circulation pipeline, maintain the daily circulation of the cutting fluid, and remove the miscellaneous oil and other impurities in the cutting fluid in time.
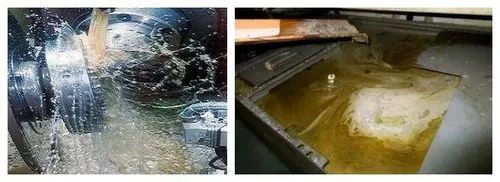
3. Resource treatment of metal cutting fluid waste liquid The establishment and implementation of a metal cutting fluid management and maintenance system can effectively improve its service life, but with the prolongation of cutting fluid use time, active ingredients continue to be lost, and microorganisms continue to proliferate, which will eventually lead to corruption, deterioration, loss of performance, and the formation of cutting liquid waste. The waste cutting fluid has the characteristics of complex composition, huge difference in properties, high stability, and non-degradation. Its COD can reach 105-106 mg/L. How to effectively treat the waste cutting fluid has become a major problem in the field of environmental protection. At present, the cutting fluid waste of domestic enterprises is mainly processed by professional companies with processing qualifications, which has high processing cost, difficult processing and high environmental pressure. The waste liquid of cutting fluid mainly contains base oil, various additives, metal ions, microorganisms and their metabolites, inorganic salts and water. Among them, water, as the dilution medium of the cutting fluid working fluid, has the largest content in the waste fluid, which is generally greater than 80% according to the mass fraction plan. Through a relatively simple process, the user separates and purifies the water in the waste liquid to meet the standard, and then continues to use it as cutting fluid dilution water, so as to realize the resource utilization of the components with the largest content in the waste liquid, which is the reduction of cutting fluid waste liquid emission reduction. A proven method. The entire life cycle of metalworking fluids should include development, use and post-processing. The development of high-performance, easily degradable and environmentally friendly cutting fluids can reduce tool wear during cutting and make cutting fluids easy to biodegrade; establish and implement a sound cutting fluid management and maintenance system to help users choose appropriate cutting fluids. At the same time, it improves its use effect and prolongs its service life; the recycling of cutting fluid waste liquid can reduce emissions and relieve environmental pressure. These are all effective ways to help the low-carbon transformation of the manufacturing industry from the perspective of metal cutting fluids, and jointly promote the realization of the "dual carbon" goal.