What should I do if the anti-foam of hydraulic oil fails?
January 03, 2022
Hydraulic systems are widely used in industrial production, construction machinery and other equipment. The main function of the hydraulic system is to convert mechanical energy into pressure energy and output work externally. Hydraulic oil is the energy transfer medium in the process of hydraulic system work. The performance of hydraulic oil has a direct impact on the efficiency and status of the transmission, and the foaming of hydraulic oil is one of the important factors that endanger the normal operation of the hydraulic system. The foam produced during the operation of hydraulic oil will cause the following hazards to the hydraulic system: (1) Unstable transmission process: The hydraulic medium is usually at a high pressure during the process of transferring energy, so the hydraulic medium is required to be incompressible. When air bubbles are mixed into the hydraulic oil, the volume of the air bubbles changes rapidly as the pressure changes, causing the power transmission process to be unstable, which in turn leads to other failures; (2) Accelerate oil oxidation: The air bubbles in the hydraulic oil increase the contact area between the oil and the air, and the oxygen in the air will accelerate the oxidation of the oil; (3) The oil cannot be sucked in: When a large amount of air is mixed in the oil, the hydraulic pump cannot effectively suck the hydraulic fluid and cannot perform external work; (4) Cause the hydraulic pump to wear: The air bubbles mixed in the oil will impact the moving parts of the hydraulic pump during the high-speed operation of the hydraulic pump, thereby causing wear.
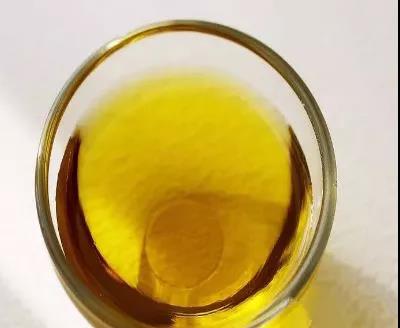
In summary, the generation of bubbles in the hydraulic system will adversely affect equipment, oil products, and operations. Therefore, it is necessary to control the generation of bubbles in the hydraulic oil and quickly eliminate bubbles. 1. Anti-foaming problem during hydraulic oil formulation development Anti-foaming agents used in hydraulic oils are generally divided into three types: silicone type, non-silicon type and compound type. From the point of view of defoaming effect, at the same dosage, the defoaming effect of silicon antifoaming agent is better than that of non-silicone antifoaming agent. However, the defoaming effect of the silicon antifoaming agent is greatly affected by the way it is added, and after long-term storage, the defoaming effect decreases significantly. The non-silicone antifoaming agent is not easy to separate out in the oil, and the antifoaming effect is still good after long-term storage, and it is not sensitive to the way of adding. Compound Anti-foaming Agent combines the characteristics of silicon and non-silicon anti-foaming agents, and the application effect is better. When adding an anti-foaming agent to hydraulic oil, not only the anti-foaming effect of the anti-foaming agent needs to be considered, but also the influence of the anti-foaming agent on the air release performance of the hydraulic oil. If there is too much air in the hydraulic oil that cannot be released in time, it will cause unstable energy transfer in the hydraulic system during use. Studies have shown that the addition of silicon anti-foaming agents will result in poor air release performance of hydraulic oil, and non-silicon anti-foaming agents and composite anti-foaming agents have little effect on the air release value. Therefore, if the air release of hydraulic oil products is poor, you can consider using non-silicone anti-foaming agents or composite anti-foaming agents. When selecting an anti-foaming agent, the compatibility of the anti-foaming agent and other additives also needs to be considered. Silicone antifoaming agent has better compatibility with various additives. When the non-silicon antifoaming agent is used in combination with the three additives of T601, T109, and T705, it can even promote the foaming of oil. The viscosity of the Base Oil also affects the anti-foaming effect. The use of low-viscosity anti-foaming agents in high-viscosity base oils and the use of high-viscosity anti-foaming agents in low-viscosity base oils can achieve better anti-foaming effects. The hydraulic oil has a variety of viscosity grades, so it is best to combine the viscosity of the hydraulic oil to choose an antifoaming agent to achieve the best defoaming effect. 2. The anti-foaming failure of hydraulic oil after long-term storage The anti-foaming performance of hydraulic fluids that use silicone anti-foaming agents or composite anti-foaming agents usually deteriorates after being stored for a long period of time. The silicone anti-foaming agent is polysiloxane (silicone oil), which has stable chemical properties and low volatility, with a viscosity of 20~10000mm2/s (25℃) and a surface tension of 21~25mN/m (35℃). Silicon-based anti-foaming agent has very little solubility in lubricating oil and exists in the form of fine particles. During long-term storage, the silicon-based anti-foaming agent particles continue to aggregate and gradually settle, and the anti-foaming agent dispersed in the oil Decrease, resulting in poor anti-foaming effect. The settling speed of the anti-foaming agent is related to the dispersion state of the anti-foaming agent in the oil. The factors affecting the dispersion state of the anti-foaming agent include the molecular weight of the anti-foaming agent, the dilution method of the anti-foaming agent, the method of adding the anti-foaming agent and the oil blending process Conditions etc. The dispersion of low molecular weight silicone oil in hydraulic oil is more stable. In order to improve the dispersion effect, kerosene is usually used to pre-disperse the silicone oil anti-foaming agent, and when the anti-foaming agent is added to the oil blending, the dispersion of the anti-foaming agent can be improved by increasing the stirring intensity and adding dropwise to obtain better Good anti-foaming effect and storage stability. By adjusting the above variables, the sedimentation rate of the silicone antifoam agent in the oil can be delayed during storage. For hydraulic oils that have been stored for a long time, it is recommended to sample before use to test their anti-foaming performance. When the anti-foaming performance does not meet the standard requirements, the settled anti-foaming agent can be re-dispersed by stirring, shaking, etc. to improve the anti-foaming performance. 3. Anti-foaming failure during hydraulic oil use During the use of hydraulic oil, various pollutants may enter the hydraulic system due to the working conditions. These pollutants can be roughly divided into residual pollutants from machine parts, external intrusive pollutants, and regenerated pollutants. Some of these pollutants have a certain surface activity, which leads to increased foaming of hydraulic oil. In addition, some oxidation products generated during the use of hydraulic oil have low surface tension, which will also cause the hydraulic oil to deteriorate its anti-foaming property. The hydraulic system has high requirements for the cleanliness of the hydraulic oil. Some additives in the hydraulic oil, including anti-foaming agents, may be filtered out by the filter elements in the hydraulic system, resulting in poor anti-foaming performance. The anti-foaming performance of the hydraulic oil should be tested regularly during the use of the hydraulic oil. When the anti-foaming performance of the hydraulic oil is poor, a certain amount of anti-foaming agent can be added to the hydraulic oil tank, and the improvement of the anti-foaming performance of the hydraulic oil should be tested. Whether the condition meets the standard requirements. If the anti-foam performance is still unqualified after supplementing a certain anti-foaming agent, the hydraulic oil needs to be replaced. Some of the measures that can be taken when the anti-foam failure of hydraulic oil fails in different situations are shown in the figure below. After long-term storage and use of new hydraulic oil and hydraulic oil, anti-foam failure may occur. By selecting the appropriate type of anti-foaming agent and adding an appropriate amount of anti-foaming agent, the anti-foaming performance of hydraulic oil can be effectively improved. In the hydraulic oil blending process, the process conditions should be controlled to make the anti-foaming agent reach a better dispersion state. After long-term storage, the anti-foaming performance of hydraulic oil should be tested before use, and appropriate measures should be taken to improve the anti-foaming performance when the oil's anti-foaming performance is found to be deteriorated. In the process of oil use, the anti-foam performance of hydraulic oil should be monitored regularly, and appropriate treatment measures should be taken in time when abnormalities are found.