Discussion on the way of low carbonization of metal cutting fluid under the target of "double carbon"
February 26, 2023
Since September 2020, when China announced at the general debate of the seventy-fifth United Nations General Assembly that carbon dioxide emissions should reach the peak by 2030 and strive to achieve carbon neutrality by 2060, relevant national departments have issued a series of guidelines on energy conservation and emission reduction around the "double carbon" goal.
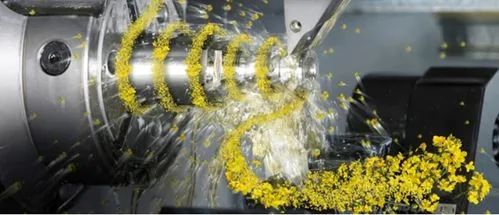
Develop environment-friendly metal cutting fluid with high performance and easy degradation As the "blood" of manufacturing industry, metal cutting fluid is one of the key factors affecting its green and low-carbon transformation. Metal cutting fluid refers to the auxiliary used in the metal cutting process, which mainly plays the role of lubrication, cooling, cleaning and rust prevention. At present, the metal cutting fluid on the market is mostly composed of Base Oil, antirust agent, emulsifier, dispersant, mildew inhibitor and other additives. The main problems are as follows: base oil and additives mainly come from petroleum products, which consume a lot of petroleum resources; Additives have certain chemical hazards, and some additives have certain biological toxicity; Improper use or management can easily lead to the deterioration of cutting fluid, affect the processing effect and worsen the working environment; The cutting fluid waste liquid has high stability, is not easy to degrade, and the environmental protection treatment burden is heavy. Therefore, using biodegradable vegetable oil or vegetable oil-based synthetic ester instead of mineral oil as base oil, and using new non-toxic and harmless additives instead of traditional toxic and harmful additives to develop high-performance and easy-degradable environment-friendly cutting fluid has become the development trend of the industry. For example, the biodegradability of vegetable oil-based titanium alloy cutting fluid is significantly better than that of mineral oil-based commercial fluid, which can effectively reduce the pressure of subsequent waste liquid treatment and reduce the impact on the environment. According to the above test results, compared with the traditional mineral oil-based cutting fluid, the vegetable oil-based cutting fluid has stronger lubricating performance and higher biodegradation rate. By replacing mineral oil in cutting fluid with vegetable oil, not only the dependence on petroleum products is reduced, but also the cutting fluid has the effect of prolonging tool life, reducing tool wear and low pollution.
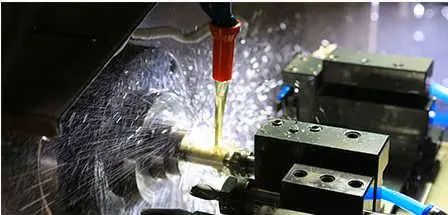
Establish metal cutting fluid management and maintenance system Even if the cutting fluid with good performance is used improperly and maintained poorly, many problems will occur, such as rust, reduced lubrication capacity, increased foam and shortened service life. Therefore, in machining, users should not only choose high-performance environment-friendly cutting fluid, but also grasp the correct use, management and maintenance methods of cutting fluid in combination with the on-site process, so as to give full play to the role of cutting fluid, so as to reduce tool wear during machining, improve machining quality, and reduce the consumption and discharge of cutting fluid. However, for most enterprises, because metal cutting fluid technology involves multiple disciplines, management is difficult, there are many problems, lack of full-time personnel who are familiar with the relevant knowledge of cutting fluid, and lack of attention or ability to the selection, use and maintenance of cutting fluid. Therefore, it is particularly important to establish a systematic and complete cutting fluid management and maintenance system based on the actual situation of users to improve the processing level of manufacturing industry and reduce consumption and emissions. The management and maintenance system of metal cutting fluid should include: selection of cutting fluid, replacement of cutting fluid and maintenance of cutting fluid. Among them, the selection of cutting fluid should fully consider the type of plant used, machine tool type, processing technology, workpiece material, tool material, diluted water quality, machine tool fluid supply system, storage conditions of oil warehouse, difficulty of waste liquid treatment, safety and environmental protection performance of cutting fluid and product cost performance ratio, and comprehensively evaluate and select the most suitable product. After selecting a suitable cutting fluid, the original cutting fluid in the machine tool should be replaced before starting to use. The replacement of cutting fluid includes: cleaning the fluid tank and circulation system, disinfecting the fluid tank and circulation system, and preparing a new fluid with appropriate concentration. After replacement, it is still necessary to maintain the cutting fluid in order to make it work well. During daily maintenance, the appearance, concentration, pH value, conductivity, water hardness, foam, rust prevention performance, microbial colony count and other indicators of cutting fluid should be monitored. If the indicators are abnormal, the cutting fluid should be adjusted in a timely manner; At the same time, it is also necessary to ensure the smoothness of the circulation pipeline, maintain the daily circulation of the cutting fluid, and timely remove the impurity oil and other impurities in the cutting fluid. After the establishment and implementation of the management and maintenance system, the cutting fluid consumption of the enterprise has been reduced by 37.5%, and the service life has been significantly extended. In addition, by selecting appropriate cutting fluid and strengthening the lubrication during cutting, the tool wear is reduced, and the tool saving rate reaches 15%. It can be seen that the establishment and implementation of the metal cutting fluid management and maintenance system can greatly promote the consumption reduction and emission reduction in the machining process. Resource treatment of waste metal cutting fluid The establishment and implementation of the metal cutting fluid management and maintenance system can effectively improve its service life. However, with the extension of the cutting fluid service time, the effective ingredients continue to be lost, and the microorganisms continue to proliferate, which will eventually lead to corruption, deterioration, loss of service performance, and formation of cutting fluid waste. How to effectively treat waste cutting fluid has become a major problem in the field of environmental protection. At present, the cutting fluid waste liquid of domestic enterprises is mainly treated by professional companies with treatment qualifications, with high treatment cost, difficult treatment and high environmental pressure. Cutting fluid waste liquid mainly contains base oil, various additives, metal ions, microorganisms and their metabolites, inorganic salts and water. Among them, water, as the dilution medium of cutting fluid working fluid, has the largest content in the waste liquid, which is generally greater than 80% according to the mass fraction plan. Users use a relatively simple process to separate and purify the water in the waste liquid, and then continue to use it as cutting fluid dilution water to realize the resource utilization of the largest component in the waste liquid, which is an effective way to reduce the emission of cutting fluid waste liquid.
For example, the water in the cutting fluid waste liquid can be recycled through the relatively simple flocculation sedimentation - membrane treatment process. Although it cannot meet the discharge standard, it can be reused as dilution water for the preparation of cutting fluid working fluid. It not only reduces the treatment difficulty and cost of waste liquid, but also recycles the water in it, reduces the consumption of water resources and the discharge of waste liquid, and further helps the manufacturing industry to reduce carbon and emissions. At present, the process has achieved a good effect of reducing the waste liquid discharge rate by 80%. In addition, copper-coated iron powder was used as Fenton reaction catalyst, and the process of demulsification - Fenton oxidation - pH callback - coagulation was used to treat waste cutting fluid, and the ideal results were obtained. In addition, the process of mechanical grating - pH regulation - oil separator - air flotation - biological tank is used to treat cutting fluid wastewater, and the effluent can be reused for production and life. The whole life cycle of metal cutting fluid should include development, use and post-treatment. The development of environment-friendly cutting fluid with high performance and easy degradation can reduce tool wear during cutting and make the cutting fluid easy to be biodegradable; The establishment and implementation of a complete cutting fluid management and maintenance system can help users select appropriate cutting fluid, improve its use effect and extend its service life; The resource treatment of cutting fluid waste liquid can reduce discharge and relieve environmental pressure. These are all effective ways to help the low-carbon transformation of manufacturing industry from the perspective of metal cutting fluid. In this process, cutting fluid developers and users should cooperate with each other to jointly promote the realization of the "double carbon" goal.