How to solve the rust problem of different metal processing oils?
November 01, 2021
How to solve the rust problem of different metal processing oils? Cutting oil is often used in metal processing and treatment processes. How to prevent metal from being corroded and rusted during processing is an important performance index of metal processing oil. Corrosion is a chemical reaction in which part or all of a metal surface peels off, dissolves, or softens. "Corrosion" includes not only ferrous metals, but also other non-ferrous metals.
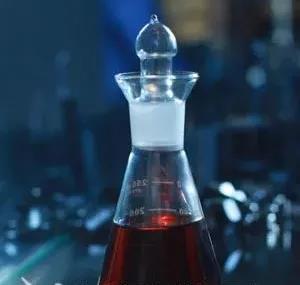
Generally, the corrosion problems encountered in the process of metal processing are divided into two situations: rust after long-term use of the machine tool and rust on the processed metal products. Metal processing oil must solve two corrosion problems: prevent corrosion of processed metal objects and prevent Corrosion of machine parts (metal parts that complete processing tasks). Four types of metals are most common in industry, steel, aluminum, magnesium, and titanium. Below we will introduce common metal processing corrosion problems for you, hoping to help you: What factors can cause metal corrosion and corrosion? In addition to the composition of the metal processing oil itself, the factors that affect rust include moisture/humidity, temperature, air quality, whether the oil is contaminated (acid, salt, other liquids such as chemical liquids, other oils, etc.), bacteria, etc. This can lead to uneven concentrations of different areas on the metal surface, cracks and nicks on the metal surface, or galvanic corrosion between dissimilar metals. 1. The rust problem of steel: Iron and steel are the most common metals with low price and high strength. The disadvantage is that they are easy to corrode (rust). Rust inhibitors commonly used in metal processing oils include amine compounds. Amines are critical to the ability to prevent rust. Pay attention to the content of amines during testing. In actual use, the factors that affect this performance include poor water quality, high bacterial content, high humidity, and acid in the air. Solution: Use oil-based cutting oil to prevent steel rust from occurring while ensuring processing quality. 2. The problem of aluminum corrosion: The density of aluminum is only about 1/3 of that of iron, and the advantage is that it is not easy to corrode. However, in some cases, aluminum will corrode, such as contact with certain metal salts (such as chloride), the PH value is too high, and contact with other metals to form galvanic corrosion. The common corrosion inhibitors for common aluminum metal processing oils are silicates, phosphate esters and so on. Solution: Use sulfurized lard as the main extreme pressure additive to reduce the proportion of chlorinated paraffin, which can effectively prevent aluminum corrosion problems. 3. Corrosion problems in magnesium processing: The density of magnesium metal is lower than that of aluminum (2/3 of aluminum), but its strength is good. Magnesium has two disadvantages: it is flammable, chemically active, and reacts with water to generate hydrogen, which is flammable and explosive. This issue is particularly important when using water-based processing fluids. Solution: You can use metal processing oil to react with magnesium flakes, collect and measure the volume of hydrogen generated, so as to judge the strength of the reaction between metal processing oil and magnesium, and pay attention to the degree of corrosion of magnesium flakes. 4. The corrosion problem of titanium metal: Titanium has the advantages of low density, high strength, the metal with the highest strength-to-weight ratio, and corrosion resistance. But the thermal conductivity is poor, so the heat dissipation capacity is not good. During processing and cutting, the heat is easily concentrated on the cutting surface and the contact surface. The elasticity of titanium metal is very good, which means that during processing, the titanium material is easy to bounce and deviate when the processing force is applied, unless the processing force is relatively large. Titanium metal is resistant to corrosion, but under high temperature conditions, stress corrosion and cracking are prone to occur. Solution: You can use the special precision cutting oil for processing titanium alloys to provide excellent extreme pressure and wear resistance under the premise of protecting the machine tool and to ensure the quality of the product. Each metal has different physical and chemical properties, so the corrosion problem should be solved according to the physical and chemical properties of the metal in use.