In addition to product reasons, semi-synthetic cutting fluid produces foam, do you know all these reasons?
September 09, 2022
With the advent of the era of Industry 4.0, metal processing enterprises pay more attention to improving the performance and adaptability of machine tools to achieve the goal of reducing costs and increasing efficiency. Therefore, the application of oil-containing semi-synthetic cutting fluids is becoming more and more extensive. Although the semi-synthetic metal cutting fluid can improve the processing efficiency, the foam problem also brings troubles to the operation and maintenance. Why do bubbles occur? Here is the answer you want to know Cause of bubbles 1- Formulation From a formulation point of view, it is unrealistic and unscientific that the cutting fluid has no foam at all. The semi-synthetic cutting fluid combines the excellent lubricity of oil and the excellent cooling property of water. It is the surfactant that makes the oil and water form a stable and uniform whole, so there must be a tendency to generate foam. Mitigation measures: Reduce foam tendency. From the formulation point of view, it is possible to select a surfactant with a lower foam tendency. On the basis of non-ionic surfactants, PO (propylene oxide) is introduced into the molecular structure to balance the foam tendency. Reduces the tendency of cutting fluids to foam. 2 - Hardness of cutting fluid water Too low water hardness will increase the foaming tendency of the cutting fluid, and increasing the hardness can help reduce the foaming tendency. Also note the definitions of soft and hard water in the product application. For example, China believes that 270PPM is definitely not soft water, but Europe will think it is soft water. Mitigation measures: For the application requirements of cutting fluid, it is necessary to unify the standard of cutting fluid water, and use cutting fluid water with higher hardness. 3 - Potential for contamination The main sources of contamination are industrial cleaning agents, cleaning agents used to clean machine tools, and even chemicals used to clean floors, or other cutting fluids with a high tendency to foam. Mitigation measures: Improve the management level and operation standard to reduce the possibility of pollution as much as possible. 4 - Loss of defoamer The defoamer is dispersed in the cutting fluid, not dissolved, so it will be gradually lost during the application process. In addition to its own loss, high filtration accuracy is also the main reason for the loss of defoamer. Mitigation measures: Regularly replenish new fluid. After a large amount of defoaming agent is lost, the anti-foaming performance of the cutting fluid itself is relatively important.
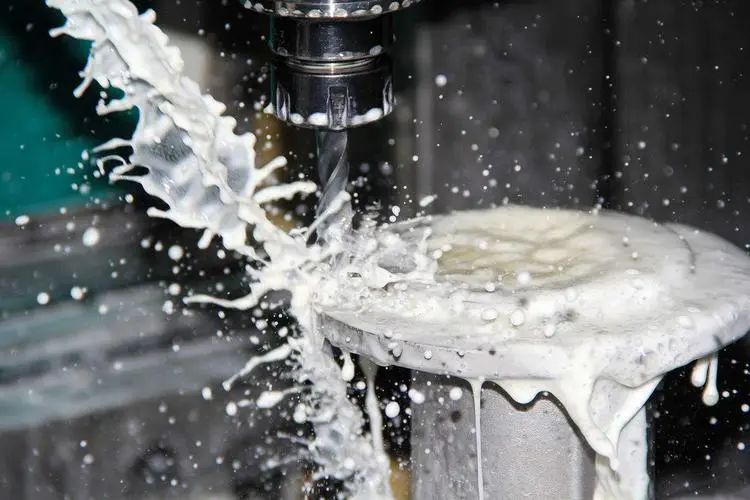
Mechanical reasons 1. - Pressure Flow Due to the improvement of processing rhythm and processing efficiency, the circulation speed and pressure of the cutting fluid of the machine tool are required to be increased accordingly, and the requirements of anti-foaming performance are correspondingly increased. Under the same conditions, the increase of pressure and flow increases the foam tendency of cutting fluid. Mitigation measures: Control the cutting fluid flow rate not too fast, and avoid too many right-angle sinks. 2 - Tank Volume / Dwell Time Due to the limitation of space, the single-machine liquid return tank is designed to be small, resulting in insufficient residence time of the liquid in the liquid return tank to release the air in the cutting fluid. The air in the cutting fluid is further sheared, which poses a greater challenge to the anti-foaming properties of the cutting fluid. Mitigation measures: increase the volume of the liquid tank and increase the residence time of the liquid return tank to fully release the air in the cutting fluid. 3 - Pump Empty Pipe leakage, especially the pipeline in front of the pump, will cause the pump suction air to mix with the cutting fluid, resulting in more foam; at the same time, it will also lead to insufficient liquid supply, gas-liquid mixing, resulting in a series of problems such as poor machining surface and burns. Mitigation measures: Check pipes regularly to avoid leaks. 4 - Processing method/filter precision High filtration accuracy will easily filter out the components in the cutting fluid that are helpful for eliminating foam, so that the cutting fluid cannot establish a balance between replenishment and consumption, and there will be a higher tendency to foam problems during operation. At the same time, the fine grinding debris during the grinding process will form a "filter cake" on the filter paper, which will make the filtration precision higher and easily lead to the problem of foam. Mitigation measures: increase the volume of the liquid tank and increase the residence time of the liquid return tank to fully release the air in the cutting fluid. Other reasons In addition to the above factors that cause the foam problem, the system bacteria, the deterioration of the emulsion, and the high temperature of the liquid tank will also be the reasons for the high foam tendency of the system.