Influence of Cutting Fluid Selection on Reaming Quality
May 22, 2022
Reaming is one of the methods of finishing holes. It is widely used in actual production, especially for smaller diameters. Compared with internal grinding and fine boring, reaming is a more economical and practical processing method. , a small amount of excess material can be removed from the hole wall of the workpiece by a reamer to improve its shape and position accuracy and surface roughness. In the long-term production practice, it is recognized that, in addition to the equipment and processing parameters that are usually concerned, in the use of cutting fluid, the selection of different cutting fluid types, the use of different cutting fluid concentrations, the cleanliness of the cutting fluid and the temperature Changes, etc., will have a certain impact on the quality of reaming. Choice of cutting fluid Currently commonly used cutting fluids are roughly divided into three categories: aqueous solutions, emulsions and cutting oils. There are certain differences in mechanical properties and process properties of different metal materials, so when reaming, it is necessary to select and use appropriate cutting fluids according to the different performance characteristics of the processed objects. When reaming medium carbon steel and alloy steel, due to the good cutting performance of medium carbon steel and alloy steel, a large amount of cutting heat will not be generated during processing, the chips are easily deformed and broken, and the tool is not easy to wear, so when choosing cutting fluid, the main The cutting fluid mainly based on lubrication and supplemented by cooling is used to reduce the surface roughness of the workpiece. When reaming at low speed, it is advisable to choose a sulfurized emulsion with a large concentration; when reaming at medium speed, a mixture of sulfurized oil and kerosene should be used to increase lubricity. When reaming stainless steel, due to the poor thermal conductivity of stainless steel materials, the chips are easy to stick to the knife, and the tool wears quickly, etc., the choice of cutting fluid should be mainly to reduce the temperature and clean the chips. Mix 3% of * and 2% of sodium carbonate with a small amount of hot water, then combine 1% of L-AN46 total loss system oil and 0.5% of ethanol, and then dilute with the remaining amount of water. Emulsified oil reams stainless steel well. When reaming cast iron, the existence of graphite in cast iron has a splitting effect on the matrix, so the strength, plasticity and toughness of cast iron are very poor, but the hardness and brittleness are very large, and there are small cracks and pinholes on the surface, which is easy to form chipping during processing. Chips are broken, no cooling is required, and the lubrication effect is not obvious. Therefore, when reaming cast iron holes, no cutting fluid is added. If one hole can be reamed twice, the surface roughness value of the workpiece can be reduced and the surface roughness of the workpiece can be reduced. The value is reduced to about Ra3.2mm. When reaming brass, since brass is composed of copper and zinc elements, the zinc content of brass generally used in the industry does not exceed 45%, so it is characterized by good plasticity, high strength and good machinability. The cutting fluid with the main lubricating effect generally uses rapeseed oil with higher viscosity. When reaming raw aluminum, that is, casting aluminum alloys, due to the poor plasticity, low strength and high brittleness of such alloys, the surface roughness value during processing is large, and kerosene or a mixture of 30% kerosene and 70% rapeseed oil can be added during reaming. Decrease the surface roughness value of the workpiece. Change of cutting fluid and hole machining quality 1. Types of cutting fluids The variety of cutting fluid directly affects the roughness value of the machined hole wall. In actual production, the selection of cutting fluid is unreasonable, which often directly causes the roughness of the hole wall to be reduced. 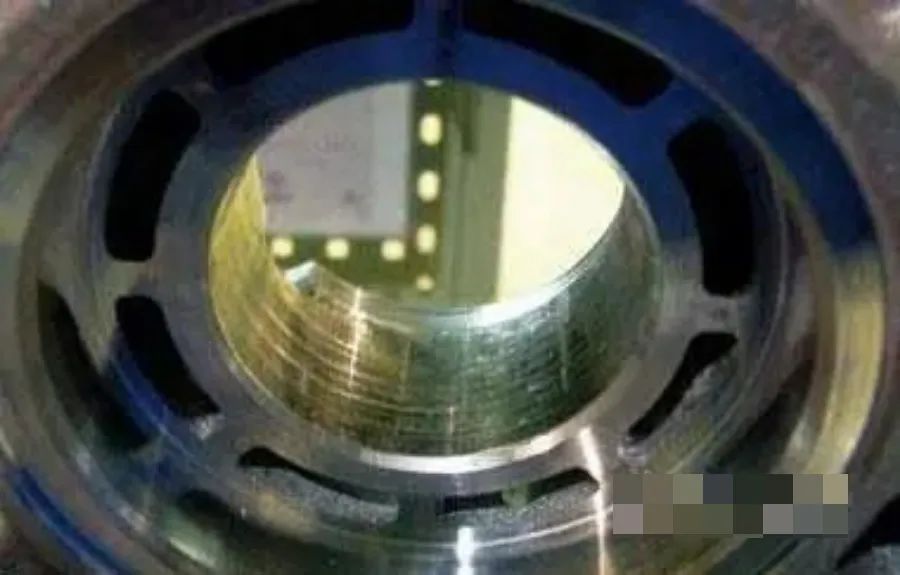
The unreasonable selection of cutting fluid often directly causes the roughness of the hole wall to decrease.
In our actual processing, when reaming holes, such as adding a high concentration of emulsion, the surface of the workpiece hole wall is as smooth as a mirror surface, the surface roughness value is very small, and the Ra can reach 0.8 ~ 1.6mm; such as adding oil for the total loss system, The color of the surface of the workpiece is black, and the surface roughness is slightly worse than that of the emulsion, and the Ra value is generally about 1.6mm; adding an aqueous solution, the surface roughness of the workpiece is the largest, and the Ra value is generally about 3.2mm. Practice has shown that: when the roughness value of the hole wall is very low, extreme pressure emulsion should be added as the cutting fluid when reaming the hole; when the surface roughness value is large, the aqueous solution should be used as the cutting fluid; if the roughness is average, it can be used. Select the oil used in the total loss system as the cutting fluid. 2. The concentration of cutting fluid The concentration of cutting fluid will directly affect the lubrication performance during processing, so the concentration of cutting fluid is a process parameter that needs to be paid attention to in actual production, that is, each processing equipment needs to set a concentration index, that is, choose the The highest concentration demand value in the coolant supply system can ensure that the tool requirements of the processing step with the highest demand are met. For example, the concentration of the cutting fluid for processing aluminum alloys is generally 8% to 10% (10% to 12% for special tools). Concentration requirements), while the concentration of processed cast iron is generally 5% to 7%. 3. Cleanliness of cutting fluid Because the machining allowance of the reaming hole is small, the chip groove of the tool itself is shallow, and the inner coolant hole of the tool holder is not large, so the cleanliness of the cutting fluid is relatively high. In our production, the same two reaming equipments process the same content. One day, the reaming quality of one equipment suddenly became very poor, and there was a phenomenon of scratching, and the hole was two holes with a gap in the middle. There is also a situation where the upper part is large and the lower part is small, and the quality of the reaming hole of another device is still very good. We searched for the reasons from the processing parameters and spindle runout, and found no problems. Finally, we considered whether it was related to the cutting fluid, so we first tried to increase the concentration of the cutting fluid from 8% to 10%, but the effect was still not good. Then we tried to replace the cutting fluid and filter the recoil of the cutting fluid. After finishing these work, try reaming, the hole wall accuracy fully meets the requirements, indicating that the cleanliness of the cutting fluid has a direct impact on the reaming accuracy. In actual production, the poor cleanliness of the coolant also directly affects the use of the tool. For example, for some reamers cooled by the inner coolant hole, there are many cases where the inner coolant hole is blocked due to dirty coolant. Once the coolant hole is blocked, the chips often cannot be discharged normally, which will cause the machined hole wall to be rough, causing The workpiece is scrapped. In addition, the dirty coolant also affects the tool and the tool holder. The tool holder in Figure 2 is because the coolant is too dirty and the chips stick to the tool holder, which increases the torque of the tool holder and causes the tool holder to be twisted. The failure consequences of being scrapped after normal use, and the workpiece has to be scrapped.
The coolant is too dirty, causing the torque of the tool holder to rise, causing it to be twisted and eventually scrapped
4. Temperature of cutting fluid The lubricating effect is that the cutting fluid penetrates into the contact surface between the tool and the workpiece to form a thin oil film, thereby reducing the friction between the tool and the cutting surface of the workpiece, reducing the adhesion of the chip and the tool and the generation of built-up edge. To form an oil film, the cutting fluid must have a certain viscosity, but the temperature has a non-negligible effect on the viscosity. As far as the whole day is concerned, with the change of the indoor ambient temperature, the temperature of the coolant will change. At the same time, the temperature of the cutting fluid in the equipment will also change due to the continuation of the processing time. Therefore, the control of the ambient temperature has It is conducive to the guarantee of processing quality, especially for finishing; in terms of the four seasons of the year, the temperature difference between summer and winter is larger, and the viscosity of the emulsion of the same concentration decreases in summer and increases in winter. Therefore, when choosing an emulsion, In summer, the viscosity should be larger, and in winter, the viscosity should be slightly smaller.