Triethanolamine is essential to improve the antirust ability of cutting fluid
January 18, 2023
The cutting fluid shall have excellent cooling, lubrication, rust prevention and cleaning functions. For water-based cutting fluid, its lubrication, rust prevention and cleaning performance is particularly critical. In order to improve the performance of cutting fluid, several or even dozens of additives, such as oiliness agent, extreme pressure agent, rust inhibitor and surfactant, should be added to the water-based cutting fluid. Triethanolamine is an important additive in water-based cutting fluid. This paper focuses on the role and application of triethanolamine in water-based cutting fluid.
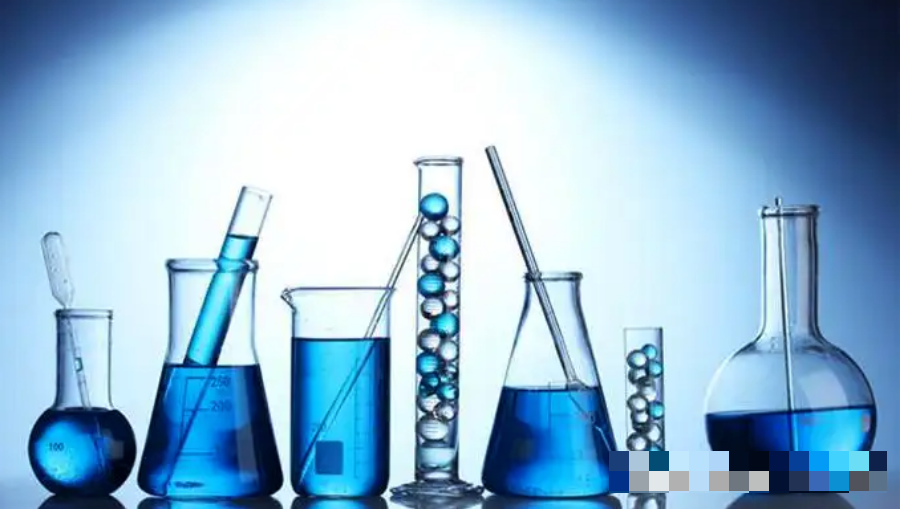
1. Properties of triethanolamine Triethanolamine, namely tri (2-hydroxyethyl) amine, is an organic compound, which can be regarded as the trihydroxy substitute of triethylamine, with the chemical formula of C6H15NO3. Like other amine compounds, triethanolamine is weakly basic due to the existence of lone pair electrons on the nitrogen atom and can react with inorganic or organic acids to form salts. Triethanolamine is formed by the reaction of ethylene oxide and ammonia, and its refined product is colorless viscous liquid. It is highly hygroscopic and becomes yellowish brown in the air. Easily soluble in water and ethanol, slightly soluble in ether and benzene. pH =8~8. 5. It cannot volatilize with water vapor. 2. Effect of Triethanolamine in Water based Cutting Fluid 2.1 Synthetic water-soluble oiliness agent
At present, most of the oiliness agents with good lubricating performance are long carbon chain substances, which are mostly water-insoluble. To add them to water-based cutting fluids, hydrophilic groups must be introduced into their molecular chains. Triethanolamine has three OH, which is well water-soluble. By controlling the ratio of raw materials, one OH in triethanolamine molecule can react with the oily agent to produce water-soluble oily agent. Oleic acid is one of the important fatty acids, but it is insoluble in water. Triethanolamine oleate can be produced by chemical reaction between triethanolamine and oleic acid (about 65 ℃). It is a commonly used water-soluble oily agent, and the higher the ratio of triethanolamine, the better the water solubility. The maximum non seizure load PB of triethanolamine aqueous solution (5%) can reach 650 N, and its friction coefficient is 0 071 。 Triethanolamine oleate is added to the cutting fluid as an oily agent, which is easy to form a physical adsorption film between the tool and the chip (workpiece), and plays a lubricating role under low load. The experiment shows that triethanolamine oleate and Ep Additive also have good synergistic antiwear effect. Adding oleic acid triethanolamine compound in the synthesis of borate ester and phosphate ester can significantly improve their extreme pressure lubrication performance, thus further improving their cutting performance. 2.2 Antirust Additive Triethanolamine itself is a water-soluble rust inhibitor. It can effectively prevent steel from rusting in a short time if used alone. Generally, triethanolamine with a concentration of 0.5%~2% has a synergistic antirust effect with water-soluble antirust agents such as phenylethanolamine, sodium benzoate, borax, and sodium carbonate. Combined use can significantly improve the antirust ability of water-based cutting fluid. However, triethanolamine is corrosive to copper, and the addition of 0.05% ~ 0.1% benzotriazole can improve the corrosion resistance to copper. Oleic acid triethanolamine is also a rust inhibitor, which is applicable to the rust prevention of ferrous metals and aluminum alloys. 2.3 Surfactant Surfactant plays a role of penetration, diffusion, stability and cleaning in water-based cutting fluid. It is an indispensable additive for synthetic cutting fluid and emulsion. Triethanolamine and fatty acid can synthesize an anionic surfactant. The HLB values of surfactants synthesized with different ratios and fatty acids are different, which can meet the needs of different water-based cutting fluids. These surfactants have good emulsifying ability. If they are used together with non-ionic surfactant alkyl phenol polyoxyethylene ether or fatty alcohol polyoxyethylene ether, the emulsifying effect will be better. Triethanolamine itself is also a non-ionic surfactant. Adding it to water can significantly reduce the surface tension of water. Adding triethanolamine to the water-based cutting fluid will help the cutting fluid soak and penetrate into the cutting (grinding) interface, so that the cooling and cleaning effects of water-based cutting fluid can be fully exerted. 2.4 Stabilizer The oily agent and extreme pressure agent added in the water-based cutting fluid are easy to be separated from water, thus reducing the role of the cutting fluid. A small amount of triethanolamine can play a stabilizing role. For example, organic borate ester is a new type of extreme pressure antiwear agent, which is formed by reacting substances with hydroxyl groups with boric acid or its compounds. The main disadvantage of borate ester is that it is easy to hydrolyze. Adding a small amount of triethanolamine in the synthesis of borate ester can inhibit the hydrolysis. 2.5 Adjust pH PH value is an important indicator of water-based cutting fluid. Too low pH value can easily breed bacteria, leading to cutting fluid corruption and workpiece and machine tool corrosion. Too high pH value will harm the operator's skin and reduce the lubricating performance. Triethanolamine is the ideal pH adjustment value of water-based cutting fluid. At the later stage of production of water-based cutting fluid, adjust the pH value of the solution with triethanolamine to prevent other additives from gelling and precipitation due to pH change. Triethanolamine can be used as neutralizer in the synthesis of phosphate ester and borate ester. 3. Application of Triethanolamine Cutting Fluid BN type water-based cutting fluid is compounded with additives such as oily agent (triethanolamine oleate), antiwear agent (sulfur-containing borate), antirust complex (triethanolamine, urea, borax, sodium carbonate, benzotriazole, etc.), and it is qualified according to GB 6144-85 Synthetic Cutting Fluid Standard (IV). The lubricating and anti rust performance is superior to the national standard. After being used for a long time in the factory, the cutting fluid has excellent performance, can significantly improve the cutting efficiency and processing quality, extend the service life of the tool, reduce the processing cost, and is harmless to the operator, with a long service life. 4. Problems needing attention in use 4.1 Triethanolamine easily reacts with nitrite to produce substances harmful to human body. Therefore, triethanolamine cutting fluid should be careful to use sodium nitrite as rust inhibitor.
4.2 When using triethanolamine type cutting fluid as grinding fluid, a slight unpleasant smell will be produced. In order to overcome this shortcoming, the addition amount of triethanolamine can be reduced, and a small amount of edible essence can also be added. 4.3 It is not easy to use cutting fluid containing triethanolamine when grinding carbide tools. Because triethanolamine aqueous solution will leach cobalt from cemented carbide tools, thus affecting the tool performance and service life.