What are the selection standards for conventional and cast aluminum cutting fluids?
February 01, 2023
The types of cutting fluids have diversified characteristics, and their performances are quite different. They should be selected scientifically depending on the processing properties, processes, workpieces and other factors. The selection principle of cutting fluid mainly includes the following aspects.
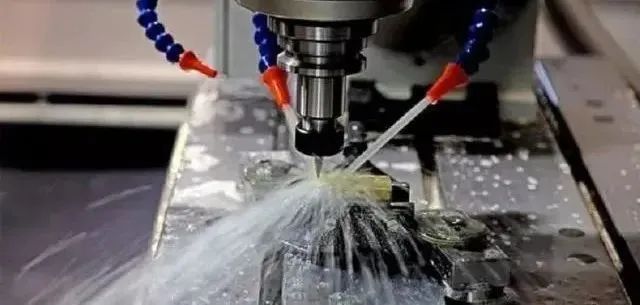
Selection standard of conventional cutting fluid The significance of the cutting fluid is the lubrication function and cooling function. On the basis of special additives, the cutting fluid also has a certain cleaning and rust prevention function, so as to comprehensively protect the machine tool, cutter and workpiece. The types of cutting fluid mainly include oil-based cutting fluid, water-based cutting fluid and emulsion. Through time study, it is found that the oil-based cutting fluid has a strong lubrication superiority, but it is not easy to cool. Compared with oil-based cutting fluid, water-based cutting fluid has weaker lubricity than oil-based cutting fluid, but better cooling performance. Conventional slow cutting requires a certain degree of lubricity. Generally, oil-based cutting fluid is selected when the cutting speed is ≤ 30m/min. However, the cutting fluid containing extreme pressure additive has certain effect when the cutting speed does not reach 60m/min in the process of cutting related materials. In the high-speed cutting state, the oil-based cutting fluid has poor thermal conductivity because it will emit a certain amount of heat, thus increasing the temperature within the cutting range. In this way, the cutting fluid will generate smoke, and even burn. At the same time, if the workpiece temperature is too high, problems such as deformation will occur, which will weaken the accuracy. Therefore, the water-based cutting fluid is more applicable. The emulsion combines the lubrication and rust prevention of oil and water, and has excellent cooling performance, so it has a significant effect on metal cutting at high speed and low pressure. Compared with oil-based cutting fluid, the emulsion has excellent heat dissipation, is easy to clean, and is economical and safer when diluted with water. In fact, except for very special processing materials, the emulsion can be well used to process light and medium load cutting. At the same time, the emulsion can also be used for most grinding processes. However, the internal problem of the emulsion is that bacteria and mold are easily generated, which will cause chemical reactions of the effective components in the emulsion, thus leading to deterioration. Based on this, a certain amount of organic bactericide will be added to the emulsion during use. The types of cutting fluids have diversified characteristics, and their performances are quite different. They should be selected scientifically depending on the processing properties, processes, workpieces and other factors. The general selection principles of cutting fluid mainly include the following aspects. Because rough machining has high machining allowance and cutting parameters, certain cutting heat will be generated during cutting, which will lead to tool wear. To solve this problem, the temperature within the cutting range should be controlled as much as possible, so emulsion and synthetic cutting fluid based on cooling should be selected. In order to control the friction between the workpiece and the tool and deepen the machining accuracy and surface quality of the workpiece, extreme pressure cutting oil and high-density extreme pressure emulsion with excellent lubricating performance should be selected for finishing. Semi closed machining, such as drilling, reaming and deep hole machining, has certain chip removal and poor heat dissipation, which will not only cause tool wear and annealing problems. Therefore, the extreme pressure emulsion and extreme pressure cutting oil with low viscosity should be selected, and the pressure and flow of cutting fluid should be deepened at the same time. In this way, it can not only provide corresponding cooling and lubrication, but also wash some chips. Common faults in cutting fluid selection NaNO2 is a common additive in cutting fluid. Cutting fluid added with NaNO2 has certain rust resistance. In the past, NaNO2 was widely used as an anti rust additive. However, NaNO2 has a strong carcinogenic effect on the human body and will have a certain impact on the health of users. At present, the World Chemical Organization prohibits the use of NaNO2 in chemicals. Therefore, in order to ensure the anti rust ability of cutting fluid products, relevant enterprises are developing new additives to replace NaNO2. It is found that the additives that can replace NaNO2 include organic and inorganic substances, the former mainly includes C3-H7-N-O, C18H34O2, RNH2; Inorganic additives include Na2B4O5 (OH)4•8H2O, MMoO, etc. In the process of R&D, relevant enterprises have developed non-toxic and harmless cutting fluids by replacing NaNO2 with the above two types of anti rust additives. Some enterprises use vegetable oil to meet the requirements of environmental protection standards and new material processing, including palm oil, rapeseed oil and soybean oil. The above Base Oil can be effectively biodegradable, and its tribological quality is superior to that of mineral oil. However, the research, development and application of vegetable oil have certain limitations, which will be affected by thermal oxidation, hydrolysis stability and high cost in the application process. The water-soluble cutting fluid of synthetic grease developed through the biological stabilization technology is a relatively mature and stable lubricating and cooling medium at this stage, and a major trend of future metal processing cutting fluid products. This kind of synthetic grease not only has excellent heat resistance and oxidation resistance, but also has strong water hydrolysis resistance and biodegradability. Selection standard of aluminum cutting fluid Cast aluminum is widely used in the processing of automobile parts and communication parts. During processing, these enterprises will generally encounter mildew caused by moldy parts after aluminum casting, which will lead to problems such as scrapping of parts and uncontrollable cost. For the above problems of customers, the article puts forward a targeted selection standard of aluminum casting cutting fluid based on the analysis of the factors leading to mildew. 1. External factors causing mildew of aluminum castings The external factors that cause the mildew of aluminum castings mainly include the following four aspects: first, the external environment in which the castings are stored mainly includes temperature and humidity; Second, the outer layer of the product has super hydrolytic substances, which will absorb the water in the air, leading to the galvanic cell corrosion reaction, which provides a basis for the growth of mold; Because of the galvanic cell corrosion reaction, the outer layer of cast aluminum precipitates alkaline compounds. On the basis of the deliquescence reaction and the temperature and humidity reaching a certain coefficient, mold grows; There are substances such as oil and plant fiber in the surface layer of aluminum castings, which will facilitate the growth of mold. If the humidity and temperature reach a certain coefficient, mold will grow rapidly. 2. Selection standard It is not allowed to use refining and modifying slagging agent containing NaCl, but refining and modifying agent with NaF composition or N2 gas refining. Do not use mold release agents containing plant additives; Replace the cutting fluid of biosynthetic grease as much as possible, such as CCF-21 series and CCF-10 products. Do not store the product outdoors for a long time to avoid dust accumulation on the outer layer of the product. The product packaging cartons stacked on the pallet shall be sealed and wrapped with waterproof bread on 6 sides; Waterproof products shall be placed in the ventilated area and sprayed with mildew inhibitor after being wetted with water. 3. Standard cases for selection of aluminum casting cutting fluid The mildew problem occurred in a company after the cutting fluid processed the cast aluminum workpiece, which has not been effectively solved. Based on the study of the company's process, it is found that the company processes parts made of AlS12 and As9Cu3Fe on the machining center. Therefore, it is recommended to select CCF-10G bio stable microemulsion cutting fluid. After using it for a period of time, the company reported the same problem. After communicating with the engineers of the company's process department, it was found that the customer had increased the processing of ASi10Mg cast aluminum workpieces. Therefore, it was recommended to use CCF-21 bio stable emulsion cutting fluid, which fundamentally solved the mildew problem of all cast aluminum processing materials in the company from the product essence. It is not difficult to find out from the above cases that the selection of cutting fluid for differential material processing has very different processing results, that is, the so-called same processing material has different process standards for the selection of cutting fluid due to the difference in the internal metal composition of the material. This needs to follow the comprehensive analysis principle of "equipment, process and material".